Aviation in Europe should be climate-neutral and sustainable by 2050. This means that climate-neutral aircraft need to be available from 2035. This requires alternative propulsion systems that are not based on fossil fuels both for main propulsion and for all auxiliary systems of aircraft.
Powerful electronic converters with an efficiency of 99 percent are needed between the battery and the engine in order to make short-haul flights efficient and environmentally friendly.
As part of the TELEV research project, the power electronics experts at Fraunhofer IZM have come up with two innovations for the drive converters of rotors in the eVTOL (Electric Vertical Takeoff and Landing Vehicle). These include insulated single-chip packages for power semiconductors and a concept for air convection cooling based on two expander mechanisms.
eVTOLs are small vertical take-off and landing aircraft. They have a wide range of applications, including inner city passenger transport, firefighting, emergency medical transport, security surveillance for police forces, and cargo transport across rough terrain.1 In the future, crewed aircraft will use hybrid-electric propulsion systems for scenarios like these. Fraunhofer IZM has been involved in the TELEV project to research aviation-compliant power electronics, distribution and control.
»For the first time, we have created an isolated single-chip package and designed an air cooling concept based on two expander mechanisms,« says Christoph Marczok by way of summary of the Power Electronics working group’s contributions to the TELEV research project. »By using silicon carbide to increase the efficiency of the switching processes, we successfully boosted the overall efficiency of the drive converter and, at the same time, minimized the space the system needs. In addition, forced air-convection cooling helps us avoid fluid cooling at the inverter, which should reduce the manufacturing costs and weight of the eVTOLS.«
Compared to conventional silicon IGBT circuits, silicon carbide (SiC) has a larger band gap (Wide Band Gap – WBG), bringing higher dielectric strength and faster switching speeds. »This enabled us to significantly reduce switching losses and achieve the required high efficiency of 99 percent for the drive inverters,« says Marczok, explaining the advantages of SiC MOSFETs. »Silicon carbide offers advantages for the electrification of both road and air vehicles.«
The single chip package
Packaged semiconductors are not a new invention. They come in different variants: Some are very inexpensive, others have a low-inductance structure, basic insulation to the heat sink, or a very good thermal path. There has not yet been a package that combines all four of these qualities. Christoph Marczok and his team have successfully managed to develop such a package and created a technology demonstrator to test the electrical switching capabilities and verify the thermal properties of the isolated single chip package.
Fraunhofer IZM’s PCB technology makes it possible to produce packages in large panel formats in very high numbers and at low cost. In addition, the flat design with electrical layers laid directly on top makes for a low-inductance structure. The SiC chip is sintered onto a ceramic substrate with very good thermal properties that help to quickly dissipate the high heat losses in the chip. The individual chips are easy to replace and the inverse voltage can be increased to 3.3 kV or higher.
The result is an extremely powerful SMD component that can be fitted easily and cost-effectively on the complete PCB using existing SMD assembly processes. Manufacturers of innovative inverter products in particular benefit from the simplified assembly and connection technology in the power module’s manufacturing. The whole process needs far less cleanroom infrastructure.
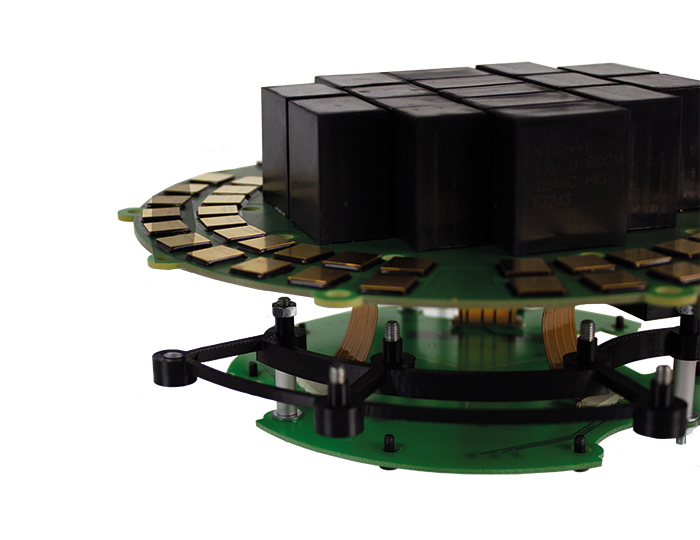
Detailed view of motor converter for Urban Air Mobility applications | © Fraunhofer IZM
Air convection cooling concept
Air convection cooling is ideal for eVTOLs, as sufficient airflow is available in any rotor aircraft. This means that complex fluid cooling mechanisms with pumps, hoses, and fluid reservoirs can be dispensed with, reducing volume and weight. But a large transfer surface is required to transfer the heat losses that occur in air-cooled systems. To achieve this, the team relies on two expander mechanisms.
The first ensures the circular distribution of heat loss over the entire circumference of the housing by physically distributing a total of 60 smaller SiC MOSFETs along the circumference. The second mechanism uses a more solid aluminium structure to redirect the vertical heat flow of the power semiconductors into a horizontal heat flow to the entire housing shell. This is equipped with cooling fins, which greatly increase the surface area and transfer the heat generated to the air flowing past.
Technical data at a glance
Topic | Technical Data |
---|---|
Total power | 130 kW |
Motor power of each rotor | 100 kW (with a total of 8 rotors) |
Max. altitude | 3,000 m |
Max. distance | approx. 100 to 200 km |
Chip used | 1200 V SiC-MOSFET |
Switch topology | B6 bridge (with 10 SiC MOSFETs per switch) |
Total number of power semiconductors | 60 units |
Number of motor phases | 3 |
Flow velocity of the air in forced convection cooling | 30 m/s |
Thermal resistance from the chip to the environment (Rth,j-a) | 3.5 K/W |
External dimensions of the housing (diameter x height) | 277 mm x 57 mm |
Efficiency | 99 % |
Power electronics for the mobility of the future
Fraunhofer IZM has been a leader in the design development and testing of packaging technologies for power electronics for over 20 years. »We are rethinking the power electronic assemblies like power switches, voltage converters, drive converters, and power modules that are needed for mobility on roads, rail, or in the air,« says Christoph Marczok about his field of work. »We use the technologies available to us to miniaturize power electronics and make them lighter.«
Left: Motor converter for eTVOLs | © Fraunhofer IZM
Right: Exploded view drawing of the inverter structure with power module PCB and driver / controller PCB | © Fraunhofer IZM
The principles of current and voltage conversion are basically the same in power electronics for aviation, road, and rail transport. However, the requirements differ depending on the area of application. »Installation space in rail transportation is less of a critical factor than in road or air vehicles,« explains Marczok. »In aviation, weight is a decisive factor. In addition, the flight altitude means that greater clearance and creepage distances must be maintained in the electrical design, which is an obstacle to miniaturization.« He points out that the electrification of the drivetrain in aircraft currently only makes sense for applications over ultra-short distances of 100 to 200 km, as larger and heavier batteries are required for longer flights.
The »Power Electronics« working group at Fraunhofer IZM has already been involved in several research projects on the electrification of subsystems, e.g. in electric rotor blade adjustment in helicopters and a large number of automotive applications. The scientists are putting their experience in packaging and their understanding of the need to miniaturize power semiconductors from the automotive sector to profitable use in aviation applications.
Save the date:
May 6 to 8, 2025: Fraunhofer IZM’s »Power Electronics« working group will be presenting at PCIM 2025 in Nuremberg, Germany.
The »TELEV« project (Technological enablement of hybrid-electric propulsion systems for manned aircraft through research into aviation-compatible power electronics, distribution and control) aims to systematically investigate the technologies needed to bring such configurations up to the performance level required for aviation.
Project partners:
Infineon Technologies AG
Liebherr-International Deutschland GmbH
Airbus Defence and Space GmbH
Fraunhofer ISE
Fraunhofer IISB
Duration: 09/2020 – 05/2024
Funding code: BMWK 20M19171
The project was made possible by funding from the BMWK via the DLR Project Management Agency for Aeronautics Research.
Download Data sheet about the research project TELEV
Sources:
1: NASA Electric Vertical Takeoff and Landing (eVTOL) Aircraft Technology for Public Services – A White Paper. Working Group 4. 2021: https://ntrs.nasa.gov/api/citations/20205000636/downloads/2021-08-20-eVTOL-White-Paper-Final_V48.pdf
Add comment