In recent years, the amount of electronic waste in the EU has risen sharply. Short product lifetimes and insufficient consumer information about the repairability of products contribute to the premature disposal of electronic equipment. The EU is trying to tackle this problem with new repair guidelines.
Another approach comes from research: The EU project PROMPT (Premature Obsolescence Multi-Stakeholder Product Testing Programme), led by Fraunhofer IZM, has developed an independent test program for the standardized evaluation of the service life of electronic consumer goods.
As early as 2020, 4.7 million tons of discarded electrical and electronic appliances ended up as waste. This figure has been rising steadily over the past three years. One reason for this is that it is often more expensive to repair an appliance than to buy a new one. Many consumers are also unaware of why their equipment breaks down prematurely or how long an electronic device is generally expected to work. This is because most of the information available on the market evaluates technical aspects, but not the expected lifetime of the product.
The goal of the PROMPT project was to provide consumers with information about the durability of electronic products at the time of purchase and to create a standardized evaluation guide.
The researchers defined three points that the test procedure must meet:
- Concrete description of how to test and evaluate a specific product
- Consideration of material state, loads, etc.
- Standards (e.g. EN4555X or established test methods)
The test procedure focused on four product groups: TVs, vacuum cleaners, smartphones and washing machines. As experts in microtechnology, the Fraunhofer IZM researchers were primarily involved in developing tests for critical subcomponents such as rechargeable batteries and electronic control units (ECUs).
A good test procedure must reflect real-life conditions
A key question that the researchers asked themselves when developing the test procedure was: How can the aging of products be simulated to reflect the real product life cycle?
Electronic products have three possible failure periods during their life cycle: early failures at the beginning of the product life cycle can usually be attributed to incorrect assembly or material weaknesses from the manufacturing process. Failures after an electronic product has reached a certain usage and service life, on the other hand, can be attributed to component wear. In the middle phase, these are usually overload failures.
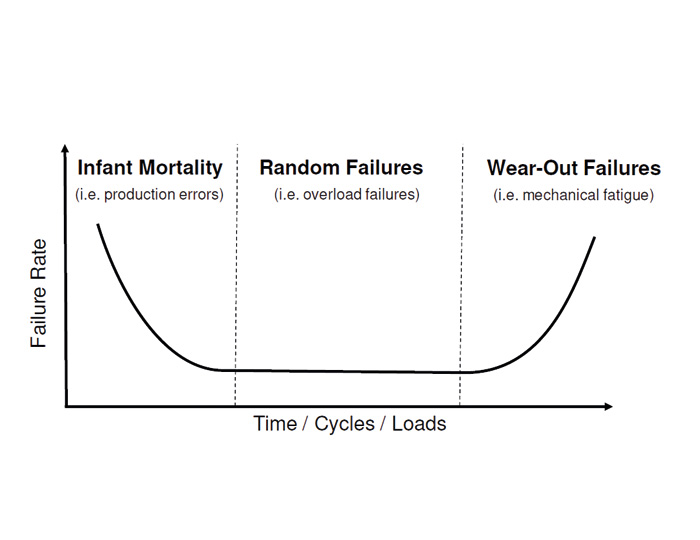
The »bathtub curve« describes the probability distribution over time with which components can fail. | © Fraunhofer IZM
PROMPT’s primary goal was to identify application-specific failure sources for the test procedure. This is because, as Olaf Wittler, senior scientist in the »Technology Reliability Simulation« department at Fraunhofer IZM, explains, a test procedure is only really useful if it maps the real loads that lead to the relevant failure types on the relevant components.
In the PROMPT project, these relevant components are called »priority parts«, which are based on the EN 45554:2020 standard. According to this standard, a »priority part« is defined on the basis of three criteria:
- The likelihood that the part will need to be replaced or upgraded
- The suitability of the part for re-use
- The functionality of the part
Product group analysis: Electronic components under the magnifying glass
Based on this definition, the researchers began collecting data for the four product groups. For technical facts, they relied on product data sheets and established test series from consumer advocacy organizations. But the project also included surveys of consumers.
»The surveys provided data on the failures of each product group and how often they occurred,« explains Daniel Hahn, research associate at Fraunhofer IZM. »Take washing machines and smartphones, for example. With washing machines, it was mainly the electronics that failed. In the case of smartphones, it’s the battery rather than the electronics that stands out. In each product group, only a limited number of components are responsible for the majority of failures. It was important to identify these weak points and tailor the test procedure accordingly. Ultimately, this enables application-oriented, meaningful results.«
Premature aging in the climate chamber
Based on the data collected, one of the biggest challenges was the length of the test series. Durability tests, such as those typically conducted by consumer advocacy groups for washing machines, last several months or even up to a year. Such tests are costly and labor-intensive and can therefore only be conducted on a small scale.
However, they do not fully reflect the real-life use cycles of consumers and the real-life aging of the product. As Daniel Hahn explains, in everyday life, washing machines are often located in bathrooms or kitchens rather than in cool, dry rooms such as those in laboratories. The electronics built into the appliances are constantly exposed to moisture and heat. In addition, the load is not constant, but intermittent – in the case of the washing machine once or twice a week. Over a long period of time, this stresses the electronic components and leads to failures. This is a fact that is rarely noticed in normal endurance tests, because the electronics can operate under ideal conditions. In order to make an accurate statement about the service life of the equipment, it is necessary to simulate not only the stress on the mechanics, but also the stress on the electronics.
While the mechanics have been tested in this way up to now, the researchers at Fraunhofer IZM and Stiftung Warentest have succeeded in simulating the wear and tear of the electronic components by artificially aging them in a climate chamber.
For washing machine control units, for example, this meant the following test procedure: The test is based on the requirements of DIN EN 60068 and tests the component in three consecutive climatic chamber runs:
- Temperature storage (static temperature exposure)
Examination of the degeneration of the material properties - Temperature cycle (dynamic temperature effect)
Examination of the degeneration of the seal/protective layer
Examination for joint failures - Humidity storage (moisture ingress)
Investigation of corrosion and electrochemical failure mechanisms
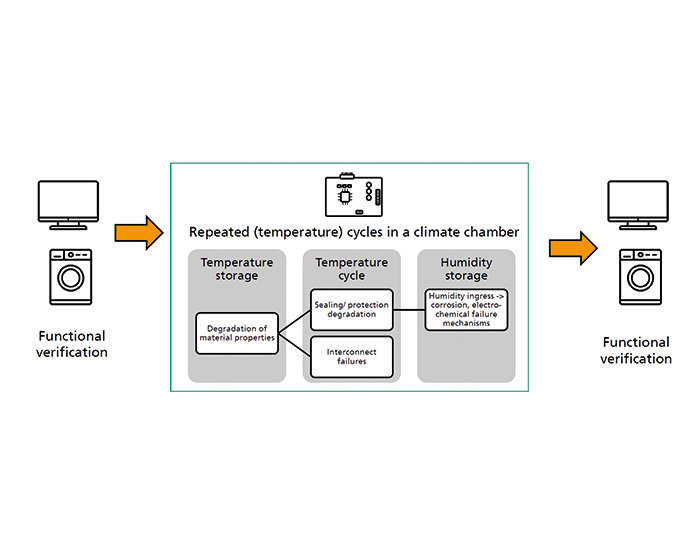
A series of tests was developed for the ECUs that takes into account application-related problems such as heat and humidity. | © Fraunhofer IZM
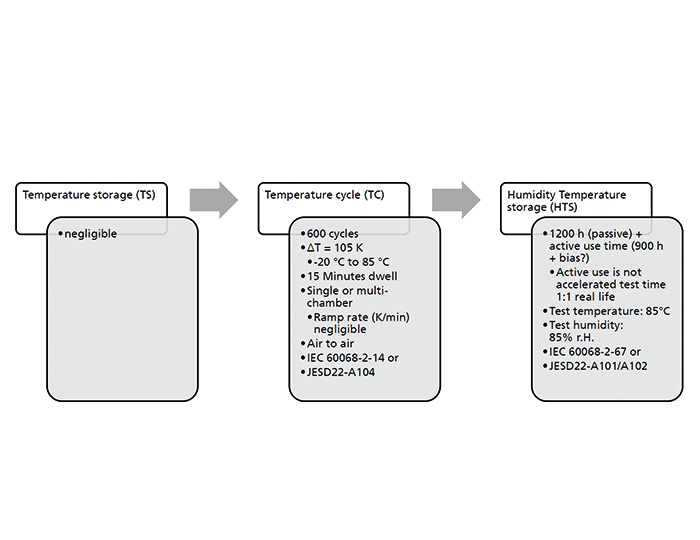
Defined test conditions for the ECU test series developed in the PROMPT project. | © Fraunhofer IZM
While the static temperature effect on the ECUs was largely negligible, the ECUs were exposed to temperatures between -20°C and 85°C with temperature changes of 105 Kelvin during 600 cycles of dynamic temperature exposure. For humidity storage, 1,200 hours of passive use plus approximately 900 hours of active use were simulated and observed at a test temperature of 85°C and 85% humidity.
This model was followed by a series of tests based on existing standards for other electrical components, including smartphone batteries. Generalization was another step in the PROMPT project.
»It is important to be able to apply a test procedure to products from a wide range of manufacturers,« explains Daniel Hahn. »The generalization of the test procedure was a central point of the project in order to guarantee the feasibility for all EU partners and to keep the test procedure up to date.«
From research to practical application and regulation
PROMPT was completed in 2023. The developed test method can now be used by consumer protection organizations. But according to Olaf Wittler, this is not the end of the story:
»The next step is to develop a common exposure profile with the manufacturers so that there is an overarching standard. This would not only be useful for consumer organizations and future research projects, but would also make it easier for consumers to make comparisons.«
According to the researchers, regulations and standards will also play a greater role in the future. After all, manufacturers need guidelines and rules for design and construction in order to make defined statements about the durability or reparability of a product.
One thing the project has shown is that testing procedures are costly and time-consuming in order to achieve good results. But Olaf Wittler also sees a solution for this in the future:
»As digitalization progresses, a kind of digital twin of the electrical device is conceivable,« he explains. »With our test method, we have not only developed statements about the reasons for the premature aging of products but have also identified sources of error. This data could be used for a digital twin and thus improve the longevity, reliability and reparability of the products.«
PROMPT is a project funded and carried out within the framework of the European Union’s Horizon research and innovation program under grant agreement No 820331.
Project leader: Fraunhofer IZM
Project partners:
Delft University of Technology (Faculty of Industrial Design Engineering)
Consumentenbond
Organización de Consumidores y Usuarios (OCU)
Stiftung Warentest
Test Achats/Test Aankoop
Union fédérale des consommateurs (UFC-Que Choisir)
European Association for the Coordination of Consumer Representation in Standardisation (ANEC)
Bureau Européen des Unions de Consommateurs (BEUC)
International Consumer Research and Testing (ICRT)
Reparatur- und Service-Zentrum (R.U.S.Z.)
iFixit GmbH
Duration: 2020 – 2023
Add comment