E-Textiles have been under development for almost two decades, but still have not reached a wide market. One of the reasons is their deficient usability which leads to a low user acceptance. Especially for textile-integrated conductor tracks, which exhibit a higher level of integration into the textile substrates, washability constitutes one of the key requirements.
Sigrid Rotzler researches the influence of the washing factors: time, temperature, chemistry, and mechanical action on the reliability of conductor tracks as well as ways to improve the washability of e-textiles.
Fraunhofer IZM has more than 15 years of experience in the field of electronic textiles. Fundamental research is particularly done in prototyping, damage analysis as well as contacting and textileintegration technologies. Applications like US welding, lamination and adhesive bonding are part of the expertise.
The definition of an e-textile or ‘smart textile’ includes any textile with integrated electronics or computers, which enables the textiles to react and adapt to external stimuli and to interact with their surroundings. E-textiles can be classified depending on the level of integration of the electronics into the textile base. The stage of adaption implies the electronics are fully detachable from the textile. (Seamless) integration describes electronics permanently embedded at yarn, textile, or product level. The stage where electronic and textile components are merged on a fiber level is called combination. Most prevalent in the market today are the stages of adaption, integration, and intermediate stages, where several components can be detached while others are non-removable.
With a wide range of possible applications, many e-textiles are designed to be wearable, worn close to or on the body. The ideal wearable is defined as a sustainable, easy to use and operate, highly comfortable and machine washable product with excellent computing capabilities and data security-standards. As these requirements are much higher than the ones that either electronics or textiles need to fulfil on their own, most e-textiles on the market do not meet all of them completely. The electronic components for e-textiles need to be integrated in a way that maintains the substrate’s textile-typical properties. Professional opinions consider washability as the key aspect for wide-ranging acceptance and the success of textiles.
What is washability?
Sigrid Rotzler: Washability stands for the ability of a (textile) product to withstand a specified washing process for a number of cycles corresponding to the intended use of the product, without functional impairment, safety hazards or damage to the utility value. The washing process aims to restore the serviceability of a textile after a use phase through the removal of soil, odour, and germs. Any washing process depends on the four interdependent factors time, chemistry, mechanical action, and temperature. The challenge is to avoid secondary washing effects like shape or colour changes. Additionally, washing damage to electronic textiles can lead to customer safety issues.
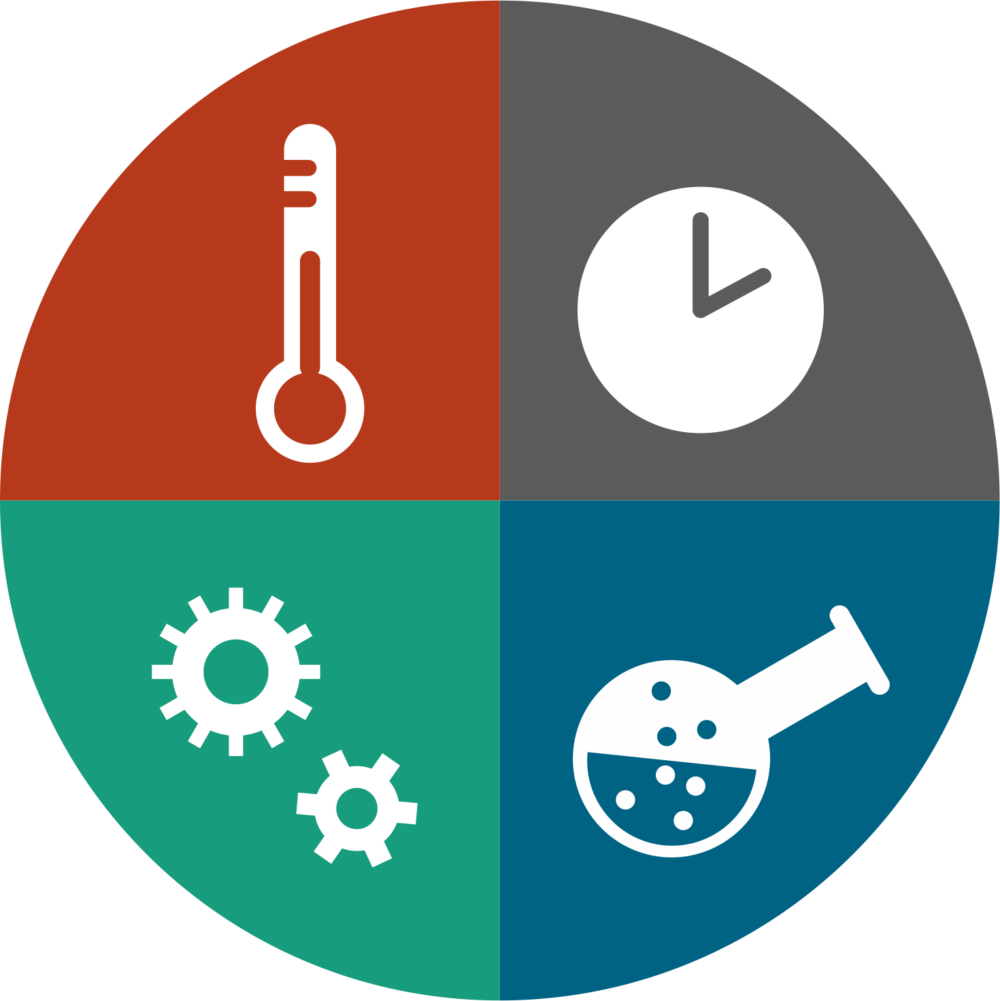
Are we talking about a normal washing machine?
Sigrid Rotzler: That depends on the product that needs to be washed. Hospital bed linen and some types of work wear must of course survive the wash cycle in an industrial washing machine. Meanwhile regular clothing only has to withstand a household washing machine. The required number of washing cycles also depends on the product: underwear for example is usually washed after every use, but an outdoor jacket is only being washed around 4-5 times during its lifecycle.
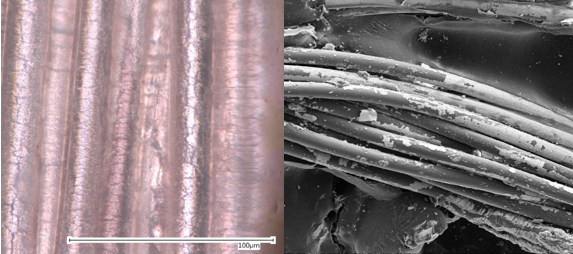
What kind of products do we test at the institute?
Sigrid Rotzler: At Fraunhofer IZM, we mainly deal with normal household laundry because a lot of e-textiles and textile-integrated electronics are targeted at the average consumer – who owns a household washing machine.
Can you name some examples?
Sigrid Rotzler: Some textile-integrated electronics do not need to be washable, such as smart seats in the automotive industries or electronic carpets or curtains as well as disposable items like smart bandages. Clothing containing electronics and other wearable e-textiles, on the other hand, needs to be washable. If e-textiles cannot be used and cleaned in the same way as regular textiles, their usability is insufficient.
For which industries is washability particularly important?
Sigrid Rotzler: Medicine and sports are important areas of application for e-textiles. In the medical industry, hygiene is very important. Sports clothing and equipment tends to get sweaty during use and needs to be washed frequently.
E-textiles have existed for many years. Why is the topic of washability only now becoming so important?
Sigrid Rotzler: E-textiles have been around for a while now, that is right. In the beginning, they often only reached a prototype stage, with demonstrators that did not need to be washed. The level of integration was quite low, with a large degree of removable electronic components, reducing washability requirements. Technological progress has led to fully integrated electronics that need to withstand washing procedures along with the textile base. E-textile developers want to bring their products from niche applications to a wider market, which makes overcoming the hurdle of washability very important. To test the washability of e-textiles, standards are required, though – to compare the washing reliability of different products, and to communicate the washability results to consumers, facilitating purchase decisions.
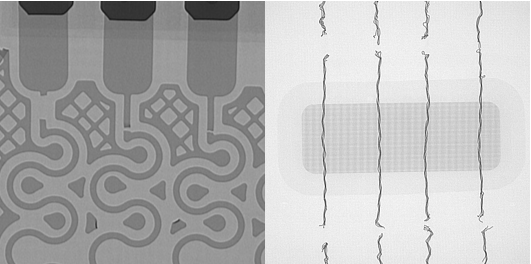
Can you tell us some more about standards?
Sigrid Rotzler: ISO 6330 is a standard from the textiles industry that provides different washing procedures for textiles. Even though it does not cover electronic components, in the absence of e-textiles specific standards this ISO 6330 standard is often used for e-textile wash testing.
To overcome this lack, I joined the IPC standardization efforts for e-textiles. Since January 2020, I am vice chair of a standardization group that develops a new reliability and washability standard for e-textiles. We started with the definition of e-textiles, wearables etc. and the establishment of product categories.
Five areas of application were defined: fashion, sport, protective equipment, medicine, and military. Additionally, we defined reliability levels. Depending on the product, different reliability requirements arise. A T-shirt with integrated LEDs or a medical bandage have very different use cases and resulting requirements and therefore need different testing protocols.
The next important step is to determine which requirements and which categories are of importance for the industry. We intend to finish the standard by the end of 2022.
Add comment