Mental health is an issue that is increasingly on the radar for many people, including people suffering from epilepsy, for whom many everyday situations can bring completely new challenges. Researchers believe that aid may come in the form of e-textiles. Pauline Stockmann, a working student at Fraunhofer IZM, shows how electronics in fashion can reduce stress and support epilepsy patients with her collection E-MERGENCE.
In her collaboration with Fraunhofer IZM, she designed five different outfits as part of her bachelor’s degree. She wanted to know what challenges and solutions there are for e-textiles in terms of sustainability, and what types of epilepsy might benefit from e-textiles as a therapeutic medium on the psychological and physiological level.
To answer these questions, she used a toolkit developed at Fraunhofer IZM to integrate a set of components in her garments with the help of an e-textile bonder. In her interview with RealIZM, Pauline Stockmann speaks about her inspirations, e-textiles and sustainability, and why there should be more electronics in fashion in the future.
To start, can you tell us a bit about your collection?
Pauline Stockmann: The E-MERGENCE collection was created as part of my bachelor dissertation. As a fashion design student at the Berlin University of Applied Sciences (HTW), I was already familiar with e-textiles, especially through my work as a student trainee at Fraunhofer IZM Berlin. So when it came to finding a topic for the thesis, this was an obvious choice. I spoke to my colleagues from the “System-on-Flex” working group, and ultimately this led me to design this collection.
I created five outfits, all dealing with the topic of epilepsy and mental health. They use electronic components and manufacturing techniques developed in the Textile Prototyping Lab (TPL) and the “System-on-Flex” department at Fraunhofer IZM – mainly the TPL toolkit and textile bonding. This is also what the name E-MERGENCE stands for. On the one hand, it hints at the fact that this is an e-textile collection. On the other hand, it is also about underlining the complexity of the work in terms of how interdisciplinary it is and how it cuts across different subject matters.
“E-MERGENCE” describes the complex functionality and progressive development of e-textiles as well as the interplay of the various disciplines involved. However, the term also stands for how my bachelor dissertation brings together the many topics from e-textiles and sustainability to epilepsy.
However, it was not just about finishing the designs. It was about pursuing innovative approaches and solutions for how our technologies can be used (through testing and research). How do you integrate conductive materials into fabrics? How can techniques like printing, embroidery, or cut construction be used to integrate electronics? What appealed to me was the idea of finding an application for e-textiles that has aesthetic and innovative value, using a range of technologies from Fraunhofer IZM. In that sense, the collection also has an experimental character in its scope. For example, it works with statistics about the weather as well as very specific findings from behavioral therapy with epilepsy patients or people with anxiety disorders.
When it comes to design, people often ask about inspirations. Can you tell us a bit more about your process? Where exactly did the idea behind E-MERGENCE come from?
Pauline Stockmann: My work at Fraunhofer IZM contributed a lot to my creative process. The Institute celebrates its 30th anniversary in 2023, and my supervisor suggested using that as inspiration. To show what the research institute has done in the last 30 years for the advancement of microelectronics and what is now possible thanks to it. The retrospective of the Institute’s findings and the evolution of e-textiles had a significant influence on my creative process. It always struck me how similar certain biological and electronic processes are. Organisms and computers have a lot in common. I wanted to use that in the collection.
Left: “The Blue Black” | Right: “All-Weather Trench Coat” (without coat)
The design of the collection is inspired by electronics and neuronal networks | © Francis Viebeck
Nerve cells and neuronal networks also served as inspiration, as they can be emblematic for how the TPL toolkit works. For example, temperature sensors can “sense” the weather and other modules can initiate a response in the sense of how temperature behaves in the garment. Or you can have LEDs that map certain emotional states or reactions. The print designs on the fabrics are also inspired by this, as are the many materials that can be used in electronics.
The collection is designed to be versatile. The starting point was the management of epilepsy, a chronic condition affecting the nervous system that has to be treated very individually and therefore – generally speaking – requires different starting points in therapy, for example through stress management. Non-verbal communication also plays an important role, so in the “Empathy” outfit, for example, two people are wearing garments that can interact with each other by sending data and thus inform their wearers about each other’s stress level via color impulses. Sensors that measure skin resistance on the palm of the hand and LEDs that visually display these states are also used for this purpose. Data transmission is contactless, using infrared light. The outfit celebrates a classic stylistic device in a new way in smart textiles and alludes to the transmission of information between nerve cells.
Left & Right: In the “Empathy” outfit, two pieces of clothing communicate with each other | © Micha Omni
Were there any other technical components that were used in the collection?
Pauline Stockmann: Yes. I also worked with textile printed circuit boards (TexPCBs) in my designs. These are printed circuit boards that can be laminated onto fabric, which consist of nanosilver-coated fibers and form a dynamically resilient and electrically conductive base material. Nonwoven fabrics are preferred for TexPCBs, as these allow a wide range of applications.
In the collection, TexPCBs were mainly used for sensors due to their unique properties and the customizability of their designs. And as with the TPL toolkit in general, the TexPCBs are made to be detachable.
Some elements of the TPL toolkit were also attached using e-textile bonding, a composite method developed at Fraunhofer IZM. In textile bonding, electronic components are bonded to the textile using heat and pressure.
The fact that things can be reversed or taken apart again seems to play an important role. Can you explain why?
Pauline Stockmann: Reversibility has mainly a sustainability background. The problem with e-textiles today is that they complicate sustainable approaches, rather than encouraging them. When you create an e-textile, you join a range of different materials together. If you then want to dispose of that garment because it is broken, things can get complicated.
Many garments are made of combinations of materials that are difficult or impossible to take apart, making recycling difficult. When electronics come into play, this becomes even more complicated. So the fact that you can detach or replace the individual components of my collection as needed was very important to me. I also made sure to work with mono-materials made from natural fibers, recycled polyester or deadstock, and to use digital printing in a way that saves water and other resources.
As a contacting method, textile bonding also comes into play more in this sense, because the bonded contacts are more reliable, but also reversible. It’s all about circular design – in other words, the idea of thinking about the entire product cycle right from the start. This starts with the textile fibers and ends with the disposal of the garment.
You mentioned the TPL toolkit several times – why exactly does it offer so much potential for such projects?
Pauline Stockmann: The TPL toolkit was developed at Fraunhofer IZM in the TPL – the Textile Prototyping Lab. It is there to make it easier for designers to integrate electronic components into their projects. The prototyping kit consists of electronic modules, sensors, or LEDs that can simply be embroidered/sewn or bonded onto textiles.
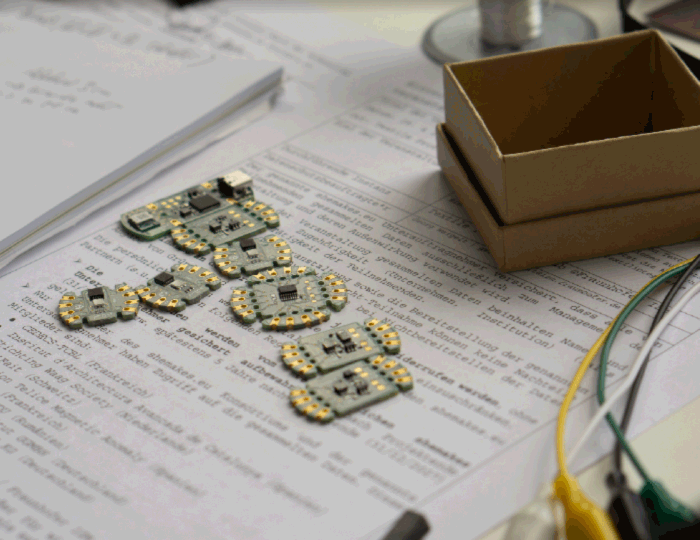
Individual components of the e-textile construction kit | © Fraunhofer IZM
In my case, I used modules to make certain processes visible or to give the garments a practical use. For example, in the outfit “Dress to Distract”, I was inspired by behavioral therapy. The electronic component in the turtleneck uses motion sensors to provide a way to take active action. In stressful, challenging moments, it can be beneficial for users to initiate calming or distracting sequences that are played out using vibration motors.
Or see the “all-weather trench coat.” The change in air pressure and humidity is measured by a sensor and visualized by a subtle change in color – orange and blue – on two embroidered pieces on the pockets. Since people with epilepsy can be sensitive to weather changes such as air pressure that can even trigger a seizure, the trench coat can provide an early warning to help them.
Left: In the “Dress to Distract” outfit, sensors sit on the arms and emit gentle vibrations to the wearer around the chest area. | © Micha Omni
Right: The “All-Weather Trench Coat” (with coat) keeps track of the weather and warns of changes in air pressure through color pulses | © Francis Viebeck
The potential of the TPL toolkit is that it makes implementation easier. I deal with electronics in my collection, but I am a designer first and foremost. With the toolkit, it’s possible for me to include what might, at first glance, appear to be complicated without in-depth electronic knowhow. This offers great opportunities for collaborations between designers and engineers or just for experimentation.
The TPL toolkit is based on an I²C communication bus and can be programmed with the freely available Arduino software DIE. The toolkit includes six standard modules:
Description | Electronics |
---|---|
Main controller board | Cortex-M0 Microcontroller/USB-Interface/ User LED |
Programmable RGB LED | Red/Green/Blue |
Inertia sensor | Accelerometer/Gyroscope/Magnetometer (10 bit) |
6× analog-to-digital converter | 6 channel /8 bit |
Temperature and humidity sensors | Humidity accuracy ±2%/temp accuracy ±0.2% |
Connects additional I²C sensors | 2-way switch |
All this sounds like a project that is already one step ahead in the future. What would be the next steps that e-textiles need to take?
Pauline Stockmann: Due to the complexity of e-textiles, this question is not so easy to answer, especially since e-textiles have already been on the market for a long time. In general, sustainability is and remains one of the most important issues. There is currently a general trend in this direction, for example in materials research, and I am curious to see how this will pan out over the next few years. In addition, in the area of e-textiles, more thought should be given to where or how to integrate electronic components. Precisely because recycling is still problematic, we need to make our products with care and attention. However, the longevity of a product can also contribute to more sustainable performance. In the case of e-textiles, this can be achieved, for example, by being easily washable or by individual components being repairable or replaceable (modularity). Fraunhofer IZM, among others, is also conducting research on washability, and the TPL toolkit can serve as an example of a modular approach for e-textiles. My colleagues from the “System-on-Flex” research group also provided input for me. It was thanks to their collaboration that the collection could be planned and realized in its complexity in the first place. The type of interdisciplinary work that I was able to enjoy at Fraunhofer IZM is particularly important when it comes to cross-disciplinary fields like e-textiles.
The research group “System-on-Flex” (SoF) at Fraunhofer IZM focuses on the further development of flexible hybrid electronics (FHE), stretchable electronics, and electronic textiles.
In the SoF group, a multidisciplinary team has been successfully investigating, developing, and validating innovative e-textiles for over 20 years. The reliable connection and contacting of textile-integrated conductors, sensors, and circuits with rigid, flexible, or stretchable functional PCB modules is its main focus, as demonstrated by the innovative textile bonding technology developed in the group.
Finally, what do you see as one of the most important contributions your collection can make?
Pauline Stockmann: For my collection, my main goal was to create connections between the electronic and the human realm. Interpersonal interaction is important, and I believe that my collection can inspire people to reflect on this. Because it was not only created in an interdisciplinary team. It also shows how easy it is to communicate with each other when you get creative.
Source:
Garbacz, Kamil; von Krshiwoblozki, Malte; Rotzler, Sigrid; Semenec, Markus; Stagun, Lars: Modular E-Textile Toolkit for Prototyping and Manufacturing. In: proceedings. 2021.
Add comment