Little to no recycled plastics are used in the making of high-end electronic devices or electrical appliances (EEE), such as computers, refrigerators, and smartphones. At the same time, these products are among the fastest growing waste categories. How can the proportion of recyclates in high-quality electronic products be increased? In the EU project INCREACE (Increase the share of recycled plastics in added value products), a consortium led by Fraunhofer IZM is developing guidelines, prototypes, and solutions for the plastics industry to implement a sustainable circular economy.
Component and EEE manufacturers, product designers, recyclers, and even the humble end consumer all play an important role in the sustainable use of plastics and the successful realization of a circular economy for high-quality electronic and electrical appliances. At the same time, all of these many stakeholder groups are confronted with technical, economic, and legal challenges.
EEE manufacturers must ensure that their products meet high quality and legal requirements. Depending on the area of application, the materials used must be flame-retardant, resistant to chemicals, and suitable for contact with food. In some cases, even more stringent medical standards must be met, and a risk of electrostatic charges must be ruled out. This is why manufacturers rely on well-known materials like “off-the-shelf plastics”.
Five products from the EEE manufacturers involved in the INCREACE project will be used to investigate whether, in what form and to what extent recycled plastics could be used in the future.
Food Contact: Pot, container, insert, and lid made of high-quality, food-safe plastic
Flame Retarded: Domestic charging station for electric cars
Chemical Restistancy: Kitchen composter used to ferment kitchen waste and bind odors
Electro Static Discharge: Heavy-duty pallet for high-performance environments or use in high-bay racking
Medical & Skin Contact: Electric sonic toothbrushes
There are many factors impacting the use of recycled plastics in electronic products, often relating to product quality or pricing on the part of both manufacturers and end consumers. For example, there are fears that:
- Recycled plastics do not meet the same quality standards as plastics made from primary raw materials.
- Electrical appliances containing recyclates cannot be sold at the same price as products made from primary plastic. The price of primary plastics is linked to the price of crude oil and is therefore relatively low compared to recyclates.
Part of the INCREACE project’s research effort focuses on the extent to which these assumptions are true and on ways to counteract them. Not every widely held assumption is actually correct. In the predecessor project “PolyCE” (Post-Consumer High-tech Recycled Polymers for a Circular Economy), a survey revealed that consumers give little thought to whether an individual product contains plastic made from primary or secondary raw materials. Instead, consumers assume that many products on the market are already made from recycled plastic. However, this assumption is simply wrong.
In 2016, only 5.3 million tons of plastic material entered recycling plants in the EU. After the recycling process, the yield of recycled plastics is usually reduced by half again.
It is important to boost the demand for recycled plastic, especially for higher value applications such as electrical and electronic equipment. Currently, recycled plastics are mainly used in construction (46%), packaging (24%) and agriculture (13%) – only 2% of recyclates currently end up in electrical and electronic equipment (EEE). This corresponds to around 80,000 tons of recycled plastics in new electrical and electronic equipment, with a theoretical market potential in the EU of around 2,100,000 tons per year.1
The Strategy for Plastics was adopted in 2018 as part of the EU Circular Economy Action Plan: Its aim is to increase the proportion of recycled plastics in new products. A key element is to ensure that ten million tons of recycled plastics are used in new products on the European market by 20252, compared to less than four million tons in 20163.
Possible ways to improve the recycling of plastic e-waste
What we would see as the advantages of plastic also leads to a variety of problems when disposing of e-waste. The variety of materials and their complex properties make it difficult to sort and recycle the material. Depending on the structure of the appliance, individual components and plastic elements can be very difficult or even impossible to separate. In addition, the composition of the plastics used is sometimes almost impossible to trace.
One problem with plastic recycling is its cost-effectiveness. Metals are an important economic driver in the recycling of e-waste. Metals can be recovered and processed at prime quality. This is different for plastics. In order to meet the different requirements and quality standards for different areas of application, a wide variety of additives (e.g. colorants, flame retardants and plasticizers) are usually added to plastics.
With current recycling methods, it is not possible to maintain a consistent level of quality of the recovered plastic. The project therefore aims to show which recycling technologies can be combined to compensate for the qualitative losses that occur during the mechanical recycling of plastics and to achieve a maximum yield of high-quality recyclates. The idea is to produce recyclates in such a way that they can be used for these applications.
Ronja Scholz and Theresa Aigner provide an insight into the potential of technical and systemic solutions in the online expert session “Recycled plastics in electronics: challenges and opportunities”:
Recording: Expert Session Recycled Plastics in Electronics: Challenges & Opportunities. Ronja Scholz & Theresa Aigner, December 5th, 2023 | © Fraunhofer IZM
Inseparable: design draft and end of life of an EEE product
The more energy the recycling processes requires, the larger the ecological footprint of electronic and electrical appliances. For the environmental experts at Fraunhofer IZM, it is therefore important to consider the issue from a sustainability perspective. This means weighing up whether an investment in sorting the waste is worthwhile. Clean waste streams require less costly recycling. But then again, might coarser sorting and more complex recycling processes be the better choice?
In addition to technical aspects, social aspects are also examined. For example, it needs to be understood how consumers could help ensure that electronic devices are fed back into the right recovery stream. This is crucial in order to close the product cycle. Attention also needs to be paid to certain regulations that may be counterproductive. Are target recycling rates actually helpful for highly regulated use cases given current technology? Or do they indeed become a hindrance?
“We are seeing a strong interest in using recyclates in electronic products. However, we are also aware of the challenges that manufacturers and recycling companies are facing. The INCREACE project aims to find solutions for these challenges, as far as this is possible,” says Theresa Aigner, research associate at Fraunhofer IZM.
On the one hand, recyclates must meet certain standards, such as being flame-retardant, resistant to chemicals, and food-safe. The challenge for recycling companies is to extract the individual plastics that are mixed together in products. Typically, the plastics also have different colors, and each manufacturer uses specific additives. Different mixed material streams have to be recycled. Depending on the product, the appliances are made of various materials, e.g. metal, ceramic and plastic. In a first step, impurities must be removed, products shredded and metals and other materials separated for reprocessing. In a second step, recyclers specializing in plastics can sort and separate the different polymers according to density. Sorting processes with the help of sensor technology also enable pure sorting. Research is currently being carried out into innovative sorting processes, which are also being considered as part of the INCREACE project. However, the question arises as to the greater leverage effect: is it worth improving sorting and reprocessing in order to eliminate product defects? Or should the product design be fundamentally rethought? Recycling yes, but not at any price. Not to forget, trends come and go. For a while, white screens were in fashion. Then black again.
Instead of viewing end products and the plastic they contain as waste, the INCREACE project takes a systemic approach: Design for and from recycling.
Workshop “Design for and from recycling”: In February 2024, the INCREACE project team invited product designers and engineers to exchange ideas on challenges in the design phase when using recycled plastics, tools for assessing recyclability and recycling strategies for EEE products. | © INCREACE Project | Fraunhofer IZM
“Recycling should not only be considered as something that happens when a product has reached the end of its service life, but as there from the very beginning of the product design process,” explains Ronja Scholz, expert in eco-design and circular service design at Fraunhofer IZM.
One of the INCREACE research questions is: Is there already a recycling stream in place for the product in question and for its specific requirements? This is the only way to decide whether different plastics should be used or whether it is necessary to redefine the requirements to find a better recycling solution going forward. Current plastics often cannot be recovered meaningfully. The project is working to identify technical, regulatory, and social barriers and potential solutions on the EU level. It will also demonstrate that it is technically possible to reuse recycled plastic, at least if the necessary legislation is passed.
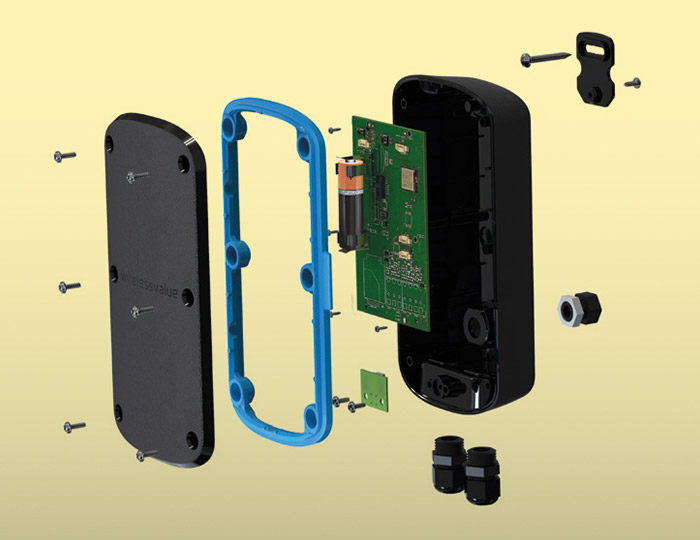
Plastics housing with design requirements for and from recycling; PolyCE Guidelines4
| © PolyCE Projekt | Fraunhofer IZM
The fact that there is no standardized EU-wide take-back system for e-waste has an impact on the nature of the proposed solutions. One key challenge facing the researchers in the INCREACE project is: Which solutions can be generalized, and which cases call for more custom answers? The same question also relates to how to recycling issues can be communicated in product marketing.
Recyclates in electronic products: A question of transparency and acceptance
Many companies fear greenwashing. The accusation of misleading advertising quickly arises when products are declared to be environmentally friendly/sustainable, but only part of the product, often a single element, is actually made from recycled material. The uncertainty on both sides – manufacturers and consumers – is great. For this reason, the research project also examines issues relating to consumer awareness and the acceptance of recycled plastics in electronic products:
- Is it advisable to label the origin of the material on the product, or is it better to use recycled materials without drawing attention to the fact? In other words, how do end consumers react when they know that a product that e.g. comes into contact with food was previously part of a computer case?
- Do general statements from manufacturers like “Our company is … in recycling” (scoring) or absolute statements like “The product consists of 20 percent recycled plastic” win the customer’s trust?
Traceability and transparency regarding the use of recyclates in electronic products are also important prerequisites for legislators to be able to introduce a quota on the market or levy punitive taxes on primary plastics. At present, it is almost impossible to verify the make-up of plastics made up of both recyclates and primary plastics.
A blockchain approach could provide a remedy: This would mean that every electronic product is given a token. The token stores information on what raw materials the device is made of and what their properties are. This would allow products to be fed back into the recycling process in a more targeted manner. Data-driven sorting using artificial intelligence (AI) could also improve the recycling of plastics.
The INCREACE project is funded by the European Health and Digital Executive Agency (HaDEA) under the Horizon Europe Cluster 4 program.
This project has received funding from the research and innovation program “Horizont Europa” under grant agreement Nr. 101058487.
Partners involved:
Fraunhofer-Gesellschaft zur Förderung der angewandten Forschung –
(Fraunhofer IZM coordinator, Fraunhofer IVV project partner), Vlaamse instelling voor technologisch onderzoek (VITO), Katholieke Universiteit Leuven – KU Leuven, Pezy Group, Plastika Skaza, Vorwerk Elektrowerke GmbH, Neste Oyj, Partners for Innovation, Mirec, Cabka Spain Sociedad Limitada, , Universiteit Maastricht, SAP SE, EGEN, Philips Electronics Nederland, Erion Compliance Organization S.c. a r.l., Cloud Selling, ETH Zurich
Fraunhofer IZM is part of the Green ICT Competence Center at the Research Fab Microelectronics Germany (“Green ICT @ FMD”) and a central point of contact for sustainable electronics.
Sources:
1: PlasticsEurope (2019) – The Circular Economy for Plastics – A European Overview (p. 26)
2: European Commission (2018) – A European Strategy for Plastics in a Circular Economy – Annex III (1)
3: European Commission (2019) – Assessment report of the voluntary pledges under Annex III of the European
4: PolyCE-E-book-Circular-Design-Guidelines-2.pdf (polyce-project.eu), p. 51
Strategy for Plastics in a Circular Economy
Add comment