Fraunhofer IZM is pushing the boundaries for extremely small lithium-ion batteries, with the tiniest battery coming in at only one square millimetre. These super-small batteries are used in tiny in-ear devices or, unexpectedly, on the backs of worker bees.
Robert Hahn from Fraunhofer IZM tells us more about the bees and why they are wearing tiny backpacks stuffed with miniature sensors. The batteries are included on board and can even be recharged by infrared light in the hive. The end result: Fully rechargeable research drones in the most original sense of the term.
The story of the bees shines a light on the technical challenges when developing small batteries and the many applications they can be used for in the future.
Let’s start at the beginning: What exactly are lithium-ion batteries and what is special about them?
Robert Hahn: Lithium-ion batteries are the most widespread rechargeable batteries today. They were first installed in mobile phones, and later also in notebooks and tablets. Now, they can even be found as the main battery of electric cars.
What is Fraunhofer IZM focussing on in the development of lithium-ion batteries?
Robert Hahn: At Fraunhofer IZM, we are focusing on these very, very small batteries that no one else can develop, except for us. To develop them, we are using our silicon wafer-level processes, which take place here in the clean room. These batteries are really very small indeed: only 1×1 mm². Because of this tiny size, a few thousand of them can be produced on a single wafer. However, there are not yet that many users who need such extremely small batteries. But we have already had a project with a large medical manufacturer who wanted to fit electronics onto a contact lens. Another project involved very small hearing aids that are placed directly on the eardrum.
At the moment, we are developing batteries that fit into very small sensors for bee research. The bees will be fitted with sensors to capture data as they fly around. Our innovation is this small housing. The battery materials we are using are actually exactly the ones used in mobile phones or electric cars. With lithium batteries, you get many subgroups and different electrolytes, and we always try to use the latest and best developments.
Can you tell us a bit more about the bees with the mini-batteries on their backs?
Robert Hahn: The project with the bees is funded by the Federal Ministry of Agriculture here in Germany and is currently still active. Our partners are a company that makes electronics, beekeepers, and people who make the hives and frames for the colonies.
And Fraunhofer IZM is producing the small batteries for this project?
Robert Hahn: Exactly, we are producing tiny batteries and, in this case, even a very small solar module that is attached to the bees. Since the bees are usually in flight during daytime when the sun is shining, the battery can be charged on the go. It would be difficult to connect the bees to a charger.
We chose silicon solar cells that are essentially similar to the solar panels you see on people’s roofs. In this case, however, silicon has the added good property of reacting sensitively to infrared radiation. Bees cannot perceive infrared radiation at all. That is why the batteries can be recharged with infrared in the hive if the time in flight was not long enough for recharging. In this way, sensor data can still be collected in the beehive.
You just said that the researchers at Fraunhofer IZM are the only ones in the world who can manufacture these super-small batteries. Can you describe in more detail how they are produced?
Robert Hahn: There may, of course, be other companies that can do this, but they simply haven’t published anything yet. One can never be sure. I could well imagine that as soon as there are more applications for these miniature batteries, other companies will turn up that can produce them. But as it is now, it is an ideal area of application for us.
The lithium in the battery is very sensitive to humid air, so the battery has to be completely hermetically sealed. Larger batteries have pretty good casings. They are welded into a composite film of polymer and aluminium, with a polymer-on-polymer weld. The polymer itself is not 100% waterproof. A few molecules always diffuse into it, but that doesn’t matter for a large battery.
With very small batteries, the story is different: Every water molecule that enters the system will react with a lithium atom, so that the capacity of the battery becomes smaller and smaller. That’s why the housing must be hermetically sealed in any case. Up to now, we simply did not have such super-small, but hermetic cases. One area where we had something of the sort is pacemakers. There are batteries that are used for implants and for other applications in the body. These batteries, however, are actually welded in with glass feed-throughs, small glass discs with a welded-in wire and a welded-on titanium housing around the unit. Metal and glass together seal well. But this lead-through alone has a diameter of at least 2 millimetres. If the whole battery is supposed to be smaller than one millimetre, this is just too large.
This is a problem; the smaller the battery, the more space the housing technology takes up and the space left for actual battery material becomes smaller and smaller. There are technologies with silicon where vias are made in the silicon from one side to the other. Copper is passed through vertically and goes through the lithium. This can also be used for normal circuits to pass through for the battery.
The battery only needs two poles. Silicon has the advantage that it can be structured far more finely than most other materials, which is why it is used for semiconductor technology. The existing structures are already in the nanometre range; you can actually structure it that finely. We don’t need it to be that fine yet, but we could, if we wanted to, make silicon sensors for the battery housing that are perhaps 50 micrometres wide. But it is important that it also remains mechanically stable. That is why the lid and the top and bottom of the batteries are about 40 micrometres thick. Although this technology is thinner than a human hair with such small batteries on a millimetre scale, most of the battery’s body is active material, such as the anode and cathode, which are filled with lithium. The casing around it is very small. That’s why we use silicon. But then, silicon is not such an ideal material for the housing, because it has to be passivated very well, as it could react with the lithium otherwise. Glass would be better, but it cannot be structured that finely.
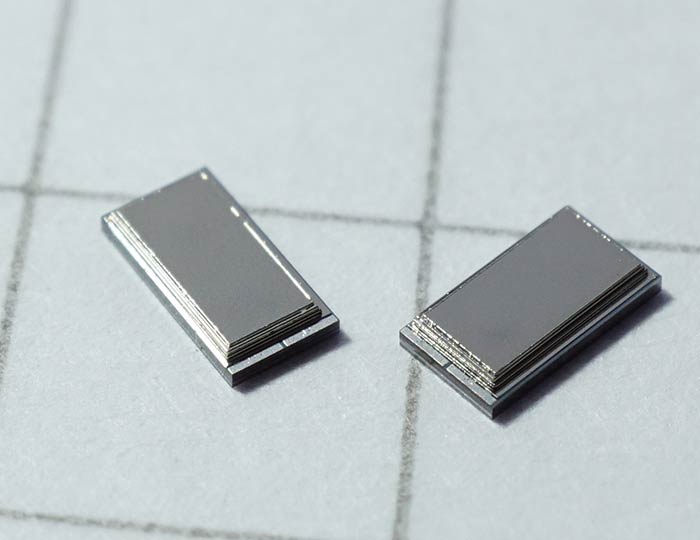
Rechargeable micro batteries 1.5 x 3 mm² | © Fraunhofer IZM
Therefore, it’s a question of making a silicon substrate that has recesses for the anode and cathode, and walls that are as thin as possible all around. We then make the hermetic encapsulation by first gluing a lid onto it, which is still a polymer. Then everything should be metallised again. After that it’s coated with a 5-micrometre metal layer and completely sealed at the end.
What were the biggest challenges in the development of this technology?
Robert Hahn: The most difficult thing about it all is that the liquid electrolyte still has to go into each of these millimetre-scale batteries. I don’t think anyone can do that except Fraunhofer IZM. Droplets of electrolyte have to be poured into each of the thousands of batteries on the wafer. When the lid is then glued on, the electrolyte must not combine with the adhesive, otherwise it would not stick properly. On the other hand, the available space should be as full as possible with electrolyte, so that the internal resistance of the battery is low, and it has high ionic conductivity. This is extremely complex technology.
Another difficulty was that batteries are not particularly temperature-stable. They can withstand 80 degrees for an hour or so, but if it is this warm or warmer for longer, they degrade quite quickly. That’s why it’s not good to leave a mobile phone in a warm car with the sun shining in. When it gets that warm, the battery ages quite a bit. It’s also bad for manufacturing if batteries get too warm.
In the clean room, with all the processes and machines that are used for the final metallisation, for example, it can quickly get over 80 degrees. These processes have to be optimised so that they work at as cold a temperature as possible. That was a lot of work.
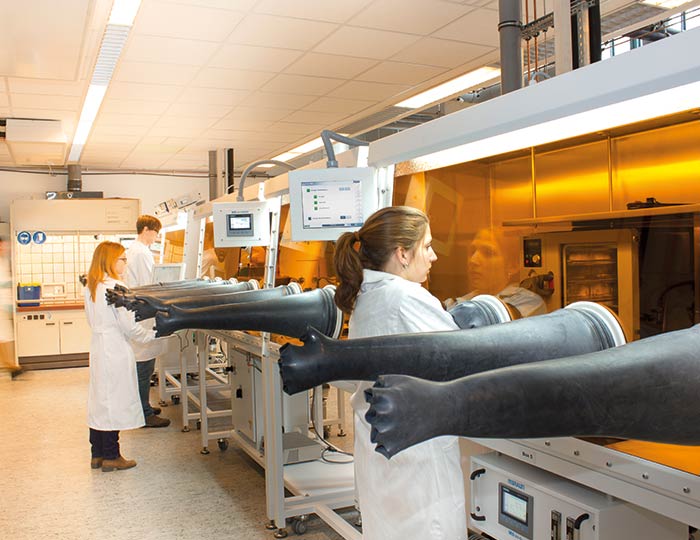
Microbattery line at Fraunhofer IZM | © Fraunhofer IZM I Volker Mai
What are future areas of application for these super-small batteries?
Robert Hahn: We can think of it as three different areas: The biggest market will probably be in medical technology. Very small electronic sensors will be placed somewhere on or in the patient’s body, for example. They would then be linked to artificial intelligence or the Internet of Things. In this way, vital parameters such as eye pressure or various other things could be measured. That is not yet possible at this point.
We have already received many enquiries about sensors for use in the mouth. They could measure certain things, for example, via implants in the gaps between teeth or in a kind of dental chip with very small electronics built in. Of course, the electronics have to be very thin, otherwise the wearer would notice. It also works in the ear. There are very small hearing aids that sit directly on the eardrum, so that you no longer have tiny versions of regular loudspeakers, but a piezo actuator that moves the actual eardrum. This is very effective and uses less energy overall.
This goes as far as implants, for example pacemakers, which are located directly in the heart at the point where the impulse should be delivered. These implants are only as big as a slightly larger grain. However, they would have to be charged differently; there are also projects to charge them directly via the pressure fluctuations in the heart itself, so that energy is generated again by mechanical conversion.
To some extent, this is still a vision for the future. But there are already products for hearing aids and braces. The technology is still a bit bigger right now, but it will probably become smaller in the future. Many things could also be considered for a possible contact lens. A display in the eye that can show you something for example, like in James Bond. Ophthalmic diseases could be treated better with such technology. There are many things that could be included, up to and including the electronic lens itself. This could replace today’s varifocals.
The second area would generally be research, where you just want to have tiny sensors that measure something somewhere without affecting the environment themselves. Even if you only want to track the temperature on a very small object, a thermocouple would perhaps already falsify the measurement. So very small sensors are used. But this applies not only to temperature, but also to all kinds of other sensors that would otherwise be difficult to get at.
In the project with the bees, for example, we want to look at the behaviour of the bees themselves and how endangered they are by environmental toxins, or how the performance of the bees can be increased. In addition, bees have already become a kind of farm animal, which can be seen as mass farming. This might be ethically questionable. Nevertheless, there is good monitoring to make sure that the bees’ welfare is not affected. The difference to other farm animals, which are bred with virtually 100% human control, is that this is not possible with bees yet, because the queen bee meets drones in the air, and this is difficult to control. But it should at least be observed better to understand what is happening. That is why such sensors are needed, which are attached to the drones.
On the other hand, bees, bumblebees, and other insects are also used as carriers. Sensors are attached to them which can take different environmental measurements. They fly around everywhere, all over the country, so thousands of measurements could be analysed, also with artificial intelligence. This is another area of research for which these small sensors could be needed.
Then there is a third area of application that will become even more interesting in the future. Electronics are increasingly present in all areas of life. Accordingly, it is also becoming more and more important that these electronics cannot be tampered with or hacked. All kinds of processes must function smoothly, which is why there are many encryption systems. The electronics should therefore be completely secure and reliable. One way to better protect current encryption systems or the keys themselves is through hardware. You could attach one of these super-small batteries to an integrated circuit on which the key is stored. The battery can then permanently monitor whether someone is trying to read the key without authorisation and destroy the key. This is part of a particularly tamper-proof electronic system and a realistic area of application for these small batteries.
So far, we have had projects in two of these areas. One is for small sensors in research, and the other is for medical technology. We have also looked at safe electronics, but have not yet had an active project on that side.
What medical technology projects have you used these batteries with at Fraunhofer IZM?
Robert Hahn: We already had a project for these small hearing aids that sit on the eardrum. The internal resistance of our battery was still a bit too high, because they wanted the battery to recharge as quickly as possible. A good way to charge it would be with a small solar cell and infrared radiation. For this, you would put an infrared plug in your ear to recharge the device. But the company wanted the recharging to work within 15-60 minutes, and we haven’t managed that yet. Now, we are working on improving the internal resistance and fast-charging capabilities.
Another thing is capacity, which gets smaller when the battery gets smaller. That’s why it’s also important for us to always use the latest materials with the highest energy density. We put a lot of work into getting the highest possible energy density in our small batteries. To that end, we employ larger or more energy-rich materials than those used in regular batteries today, in order to compensate for the scaling effect that very small batteries can also store less energy. The hearing aid, for example, must last at least 12 hours before it needs recharging.
Is cost optimisation always considered when new materials are used?
Robert Hahn: The complex process with silicon wafer production is quite expensive, but since the batteries are so small, the materials really don’t play a role. In addition, you can get quite good prices in medical technology. This preform of the hearing aid, in which our battery might be used in the next generation, costs €80 or so for a rechargeable battery, I think.
When we produce batteries on a contract basis, it’s usually a few thousand pieces. The price per battery ends up around €50 to €100. That is acceptable in any case. After all, we are not a factory, but only produce small series and prototypes.
Edited by Jacqueline Kamp
Picture: © Micro-Sensys GmbH
Add comment