Dr. Joshua Wilson, research associate in the »Technologies for Bioelectronics« working group at Fraunhofer IZM, works on non-hermetic encapsulation solutions for implantable microchips. During our exclusive tour filming in the Bioelectronics lab, he explained how biocompatible polymer and ceramic coatings could help these neural implants function in the human body for decades – without any additional interventions.
From brain to movement: The role of neural implants in prostheses
Next-generation neural interfaces will enable instant, direct, and specific communication with the nervous system. These implants will help reduce side-effects compared with conventional pharmaceutical therapies and pave the way for a broad range of new treatments for drug-resistant conditions. Until now, electronic implants such as pacemakers were fitted with hermetically sealed housing made of titanium or ceramic. However, these housings are large and inflexible, posing challenges for direct integration with fine and soft nerve tissue.
Placing the housing distally, that is, away from the actual site needing treatment and guiding leads to it also has its limitations, as these leads are prone to failure and have been the subject of high-profile product recalls by manufacturers. Moreover, simply shrinking existing solutions and placing them closer to the tissue of interest is not feasible, because the hermetic housing is rigid, which can cause potentially damaging mechanical mismatches with the soft tissue at the site. For safe and reliable microsystem implants in living tissue, these should be just as soft and flexible as the surrounding tissue.
»Distal« is an anatomical designation of position and direction and means located away from the center of the body or from a reference point, e.g. the origin of a vessel.
Experts in bioelectronics at Fraunhofer IZM are researching thin-film coatings, such as the polymer parylene C and atomic-layer-deposited ceramics. The expertise of the bioelectronics engineers flows into the »NerveRepack« research project, where a consortium of 27 European partners is working on intelligent prostheses with neural implants. The project focuses on a prosthesis for patients with forearm amputations and two exoskeletons for patients with a unilateral or bilateral paralysis of the lower limbs.
The combination of prosthesis and neural implants is intended to create an improved, more intuitive user experience. The key is bidirectional communication between the implant and the prosthesis. This means that the patient can not only control the movement of the prosthesis, but also receive information – »a feeling« – back from it. In the case of forearm prostheses, this is intended to provide tactile feedback. The exoskeletons are designed to read motor commands from spinal nerves and integrate sensor feedback from the feet in order to optimize the patient’s gait and enable the smoothest possible movement.
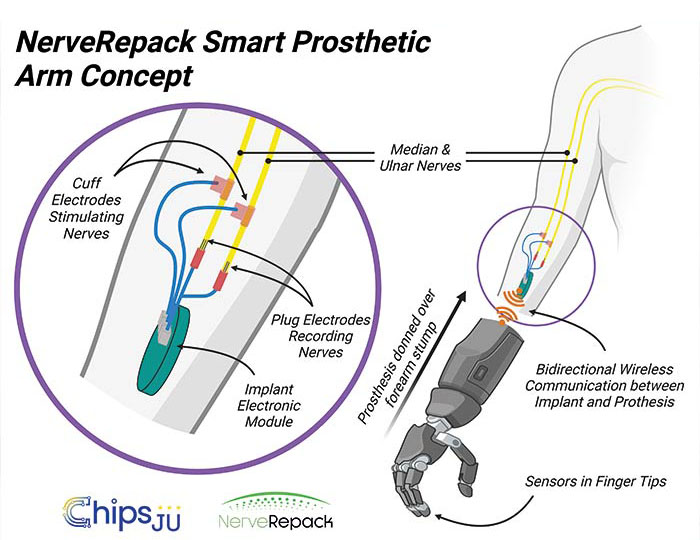
The NerveRepack prosthesis will be able to communicate wirelessly with an implant which transmits and receives signals to and from nerves in the arm. This bidirectional communication will enable more intuitive use and increased patient autonomy. The image was created with Biorender.com. © Fraunhofer IZM
Dr. Joshua Wilson, responsible for the bioelectronics laboratory at Fraunhofer IZM, invited the RealIZM team to an exclusive video tour. He explains which innovative packaging technologies Fraunhofer IZM is using to support the »NerveRepack« project and what is important for non-hermetic encapsulations for implantable electronics.
© Fraunhofer IZM
Innovative solutions for using bioelectronics in the human body
»The inside of the human body is an extremely unfavorable environment for electronic components. There is moisture, salt, and mechanical stress to contend with«, explains Dr. Joshua Wilson, bioelectronics expert at Fraunhofer IZM. These complex and dynamic conditions cause salts and water to corrode the conductive materials and implants to fail. Immune reactions can also damage the implant or cover it over with scar tissue, which severely limits its effectiveness.
Until now, hermetically sealed titanium or ceramic housings were the standard for electronic implants. »However, we are seeing a paradigm shift. In order to more safely integrate implants into human tissue, they need to be soft, flexible, and miniaturized. This is why we are researching innovative non-hermetic packaging solutions for electronic components to enable the use of miniaturized implantable medical devices«, says Wilson, explaining the research focus of the bioelectronics working group at Fraunhofer IZM. »Our approach in the ›NerveRepack‹ project is based on thin-film coatings that are thinner than a human hair and hardly increase the overall volume of the implant.«
Ceramics provide a hermetic, stable barrier in the body, but are rigid and brittle. Polymers, on the other hand, are flexible and soft. But they absorb moisture and ions. To combine the advantages of both materials, the scientists at Fraunhofer IZM are pursuing a multi-layered approach: the ceramic layers block the penetration of moisture, while the polymer layers ensure flexibility. These are thick enough to act as a mechanical buffer, preventing the spread of defects and lengthening the path for potentially penetrating moisture.
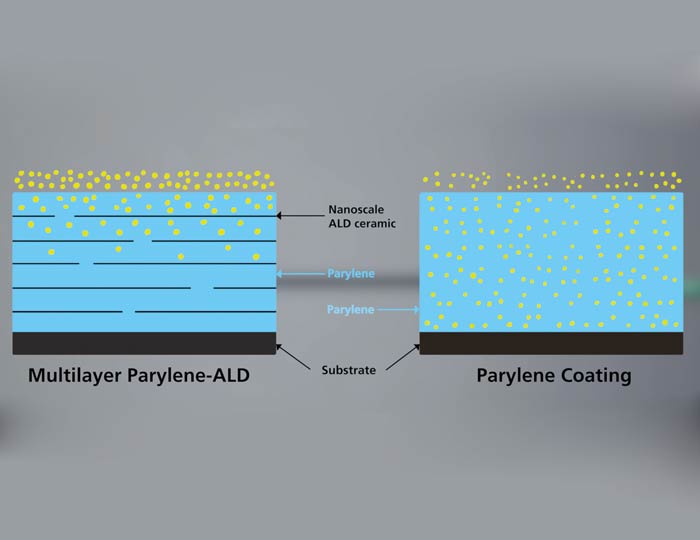
© Fraunhofer IZM I Francis Viebeck
Advanced thin-film technologies for implants
Only one machine is used to produce the structure. This avoids contamination caused by the transfer of samples between different machines.
Parylene C is characterized by
- Class VI biocompatibility
- Low water permeability and
- Excellent insulating properties.
In addition, parylene C is deposited at room temperature.
Deposition begins with a dimer in powder form, which is heated and broken down into monomers and condenses into a polymer on all surfaces in the chamber. The Fraunhofer IZM scientists use the atomic layer deposition process to produce ceramics such as aluminum oxide and titanium oxide.
In this process, the chamber is filled with various precursor substances, each of which leaves behind an atomic layer so that precisely alternating layers of metal and oxygen are created. Oxygen plasma and silane treatments are used to improve adhesion and strengthen the chemical bond to the substrate.
As part of the NerveRepack project, these coatings are thoroughly tested for their stability in a humid environment and their biocompatibility in cell cultures before they are used on humans.
Parylene C is an inert, hydrophobic, optically transparent, biocompatible, polymeric coating material.
A dimer is a molecule or molecular compound that is usually made up of two identical building blocks (monomers).
Right: Dimer in powder form © Fraunhofer IZM I Francis Viebeck
Left: Holder for the substrates to be coated © Fraunhofer IZM I Volker Mai
The NerveRepack project runs for four years and is currently halfway through its second year. The design of the implantable system, the external electronics, and the mechatronic structures are nearing completion. Materials testing for coatings continues and some components such as implantable electrodes are near completion.
Duration: 06/2023 – 05/ 2027
Funding reference: 101112347
Project page: www.nerverepack.eu/
The NerveRepack project is co-funded by the European Union under Grant Agreement No. 101112347. The project is supported by the CHIPS Joint Undertaking and its members, including additional funding from Romania, Germany, Norway, Italy, the Netherlands, Greece, Portugal, Poland, Spain, and Switzerland.
Add comment