Eine kostengünstigere Produktion von thermischen Infrarot-Sensoren als bisher würde zahlreiche neue Möglichkeiten für Wärmebildsysteme eröffnen, z.B. für Automotive- und Sicherheitsanwendungen. Forscher*innen des Fraunhofer IZM haben daher speziell für die hermetische Verkapselung von großen MEMS-Pixelarrays unter Vakuum Prozesse des Wafer-Level Packaging weiterentwickelt. Durch den Einsatz des robusten Verfahrens lässt sich der Herstellungsprozess bis zu 100 Mal schneller durchführen.
RealIZM sprach mit Dr.-Ing. Charles-Alix Manier, Entwicklungsingenieur am Fraunhofer IZM, über das EU-Forschungsprojekt APPLAUSE und die Potenziale der Packaging-Technologie.
Was waren die Hintergründe für die Weiterentwicklung der Wafer-Level Packaging Prozesse?
Dr.-Ing. Charles-Alix Manier: Unser Forschungsinstitut war Teil eines europäischen Konsortiums, das an dem EU-Projekt APPLAUSE mitgewirkt hat. APPLAUSE steht für “Advanced packaging for photonics, optics and electronics for low cost manufacturing in Europe”. Ziel des Projektes war es, neue Aufbau- und Verbindungstechniken zu entwickeln, um hochintegrierte mikro- und optoelektronische Systeme wirtschaftlich konkurrenzfähig in Europa fertigen zu können.
Das Fraunhofer IZM war an der Entwicklung von drei Anwendungsfällen beteiligt. Einer davon war, für Automotive- und Sicherheitsanwendungen eine kostengünstige Infrarot-Kamera mit erhöhten Videoraten und VGA-Auflösung mittels eines Mikrobolometer-basierten Sensors zu entwickeln. Mikrobolometer werden als Infrarot-Bildsensor in Wärmebildkameras eingesetzt.
Wie ist ein Mikrobolometer aufgebaut?
Dr.-Ing. Charles-Alix Manier: Herzstück einer Wärmebildkamera ist ein integrierter Bildsensor-Chip (Focal Plane Array), bestehend aus einer Ausleseelektronik (Readout) mit winzigen MEMS-Zellen angeordnet in einer Matrix mit einer Größe von 20.000 bis zu 1 Mio. Pixel. Jeder Pixel besteht aus einem kleinen Mikrobolometer, die in diesem Fall in einem 17 µm Pitch und mit einer Auflösung von 640 x 480 px je Array eingereiht sind. Mikrobolometer sind thermische Sensoren, die Wärmestrahlung in elektrische Signale umwandeln und elektromagnetische Strahlung wie z.B. Infrarotstrahlung im langwelligen Infrarotbereich zwischen 8 und 14 µm Wellenlänge (LWIR) messen.
Technische Spezifikationen:
17 µm | Pixelabstand zwischen den einzelnen Mikrobolometern |
640 x 480 px | VGA-Auflösung/ Anordnung der Mikrobolometer in einem Array |
12,3 x 11,2 mm2 | Seitenmaße der Kappen |
13,6 x 13,1 mm2 | Größe des Mikrobolometer-Die inkl. aller peripheren Schaltungen und IO-Pads |
Mikrobolometer verfügen über eine thermisch isolierte Membran bestehend aus einer Wärme-Absorberschicht, deren Temperaturänderung zu einer Änderung ihres elektrischen Widerstands führt. Um ihre Funktionsweise und Sensitivität zu gewährleisten, müssen Mikrobolometer thermisch isoliert werden. Hierfür brauchen sie eine Vakuum-Umgebung, die jegliche Wärmeverluste durch Konvektion verhindert. Dafür werden die MEMS-Strukturen mit einer Kappe überdeckt, die sie nicht nur mechanisch schützt sowie sauber und frei von Partikeln hält, sondern auch ein Vakuum und eine hermetische Abdichtung gegenüber der Umgebungsluft gewährleistet. Die Kappe muss gleichzeitig im LWIR-Bereich transparent sein, um eine möglichst hohe Einstrahlung auf die Mikrobolometer zu ermöglichen.
Die Abdeckung des Mikrobolometer-Arrays, das Vakuum unter der Kappe und Veränderungen des Vakuums im Laufe der Zeit wirken sich auf die Zuverlässigkeit und Leistung der Infrarotsensoren aus. Unser Auftrag bestand darin, robuste Wafer-Level Packaging-Prozesse zu entwickeln, mit denen sich thermische Infrarotsensoren in hoher Stückzahl kostengünstiger produzieren lassen.
Wie unterscheidet sich Euer Wafer-Level Packaging-Verfahren im Vergleich zu bestehenden Fertigungsverfahren?
Dr.-Ing. Charles-Alix Manier: Unser Konzept basiert auf der Herstellung von großen Kappenstrukturen auf temporären Träger-Wafern und metallischen Bondrahmen. Die Kappen werden anschließend unter Vakuum mit Device-Wafern über die metallischen doppelseitige Bondringe durch Lötverfahren zusammengefügt.
Das Besondere ist, dass die hermetische Verkapselung aller Chips auf dem Device-Wafer zeitgleich anstatt einzeln erfolgt. Der derzeitige Industriestandard in der Fertigung von Infrarotsensoren fokussiert auf das Chip-to-Chip-Packaging. Dieses Verfahren erfordert eine Vielzahl an Einzelschritte und ist im Vergleich zum Wafer-Level Packaging zeit- und kostenintensiver.
Mit unserem Ansatz können wir bei dem Herstellungsprozess von thermischen Infrarot-Sensoren einen bis zu 100-fachen Zeitgewinn erreichen, wenn man davon ausgeht, dass auf einem 200 mm Wafer je nach Chipgröße, Auflösung und MEMS-Pitch zirka 100 bis zu 250 Chips platziert werden können. Außerdem konnten wir über 95 % der Chips auf dem Wafer dicht mit Kappe versiegeln. Für Außenstehende mag dies nur ein kleiner Fortschritt sein, für uns Wissenschaftler*innen und die europäische Elektronikforschung ist es ein wichtiger Meilenstein.
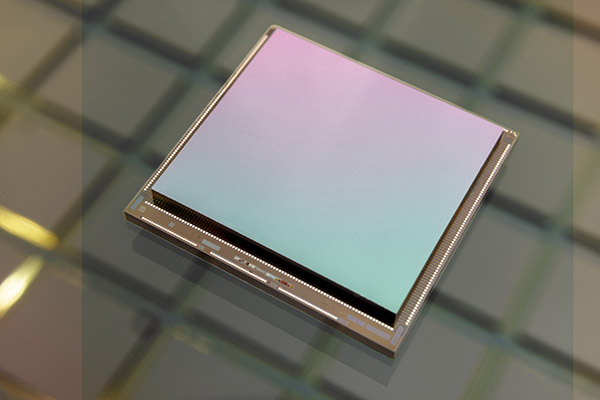
MEMS-basierter Infrarot-Bildsensor-Chip auf 200 mm Wafer-Level unter Vakuum verkapselt | © Fraunhofer IZM
Um die Qualität der Versiegelung zu bestimmen, haben wir verschiedene Pirani-Vakuum-Teststrukturen verwendet. Zunächst wurden die Widerstände gegenüber dem Druckverhalten unter kontrolliertem Referenzvakuum gemessen und anschließend mit den identischen Strukturen nach der Verkapselung verglichen. So konnten wir das Restvakuum im Inneren der Kappen ermittelt.
Die hermetische Verkapselung unter Vakuum schützt permanent die hochempfindlichen MEMS über alle weiteren Integrationsschritte bis in dem finalen Kamerasensor. Zugleich wird ihre vollständige Funktion sichergestellt und die Infrarot-Übertragung ermöglicht.
Kannst Du uns bitte den Prozess der hermetischen Verkappung unter Vakuum erläutern?
Dr.-Ing. Charles-Alix Manier: Der verwendete Wafer-Level Versiegelungsprozess beruht auf dem AuSn-Löten unter Vakuum. Um das Bonden der Kappenstrukturen zu ermöglichen, wurden diese zunächst mit Bondringstrukturen vorbereitet. Unsere Forschergruppe hat dafür Au-Ringe (Metall-Rahmen) als Bond-Interface auf allen Kappenstrukturen verwendet. Dies erfordert komplementäre Ringe aus Au+Sn auf dem Gegenstück (Device-Wafer), um den späteren Lötprozess der Kappen zu ermöglichen.
Alle Device-Wafer müssen einen elektrolytischen Abscheidungsprozess durchlaufen, um die Au+Sn-Ringe bilden zu können. In unserem Fall geschah dies mit einem semiadditiven Prozess. Dieser umfasst das Sputtern einer Keimschicht, Lithografie, Galvanisierung, die Entfernung des Resists und das Ätzen der Keimschicht.
All diese Prozesse interagieren mit der Oberfläche des Wafers und dürfen nicht auf Wafern mit freistehenden Bolometern angewandt werden. Diese sind extrem zerbrechlich und dünn, sobald sie von deren tragenden Opferschicht gelöst werden.
Es ist uns gelungen, die Ablösung des Bolometers an das Ende des Herstellungsprozesses zu verlegen – kurz vor dem Bonden der Wafer. So konnten wir den semiadditiven Prozess bereits vor dem Entfernen der Opferschicht durchführen – bevor die Mikrobolometer freistehen und zerbrechlich werden.
Nach der Ausrichtung der Wafer mittels dedizierten Marken wird die AuSn-Wafer-Bonding-Sequenz ausgeführt. Bei diesem Schritt schmilzt der AuSn-Ring und benetzt das Au-Gegenstück. Es bildet sich ein transientes Eutektikum (Flüssigphase) über den Au-Rahmen, das durchreagiert und spätestens beim Abkühlen erstarrt. Der AuSn-Rahmen kann nach dem Verbinden nicht mehr schmelzen. Grund dafür ist eine Phasenumwandlung. Die entstandene Legierung ist bis zirka 500° Grad stabil.
Nach Bonden der Kappen auf dem Wafer wird deren temporäre Klebeverbindung auf der Rückseite durch laserunterstütztes Entkleben gelöst. Im Ergebnis verbleiben die Kappen auf dem Device-Wafer und alle anderen Strukturen auf dem Träger-Wafer. Durch diese sogenannte „selektive Verkappung“ wird nur das MEMS-Feld abgedeckt. Die Randzonen der Dies z.B. die Input-Output-Pads bleiben weiterhin zugänglich.
Welche Ansätze habt Ihr getestet, um die Kappenstrukturen herzustellen?
Dr.-Ing. Charles-Alix Manier: Richtig, wir haben insgesamt zwei Ansätze untersucht, die sich für die Herstellung von großen Stückzahlen thermischer Infrarot-Sensoren eignen.
Zum einen haben wir monolithische Kappen mit einem tiefen Hohlraum durch tiefes reaktives Ionenätzen hergestellt. Dabei kamen 200 mm Silizium-Wafer mit hoher Infrarot-Transmission im LWIR-Bereich zum Einsatz. Die Silizium-Wafer wurden zusätzlich mit einer Antireflexionsbeschichtung versehen.
Träger-Wafer mit monolithischen Kappen (links) und Hybrid-Kappen (rechts), bestehend aus Silizium-Rahmen mit flachen Silizium-Deckel über AuSn-Bond gefügt vor dem Bonden auf dem Receiver-Wafer | © Fraunhofer IZM
Als zweiter Ansatz, um das innere Volumen zu maximieren, haben wir Hybrid-Kappen entwickelt. Diese bestehen aus einem Silizium-Rahmen (durchgeätzte Kavität) mit einem flachen Silizium-Deckel, die miteinander über metallische AuSn-Bondringe zusammengefügt werden.
Monolithische Silizium-Kappen (links) und Hybrid-Kappen (rechts) auf Device-Wafer dicht gebondet | © Fraunhofer IZM
Publikation:
Zoschke K., Manier C. A., Oppermann H., & Other (2023): Wafer Level Capping Technology for Vacuum Packaging of Microbolometers, vorgestellt auf der ECTC 2023, Orlando/USA
Add comment