RealIZM sprach mit Prof. Martin Schneider-Ramelow vom Fraunhofer IZM über die Ergebnisse des DFG-Forschungsprojektes »AlCuBo«.
Wie entstand die Idee zu dem Projekt »AlCuBo«?
Prof. Martin Schneider-Ramelow: Ich komme aus dem Bereich der Materialwissenschaften, insbesondere der Drahtbondtechnik, hier am Fraunhofer IZM. Bei meiner Arbeit mit dem Forschungszentrum Strangpressen der TU Berlin, unserem Partner für dieses Forschungsprojekt, habe ich festgestellt, dass die kleinsten metallischen Drähte, die sie durch Strangpressen herstellen können, nur 500 Mikrometer dünn sind. Das entspricht dem Durchmesser der größten Drähte, die wir für das Bonden in der Leistungselektronik verwenden. Drahtbonden wird in über neunzig Prozent der Leistungselektronikmodule angewendet.
Unser Ansatz ist es, neue Verbundmaterialien für Dickdraht-Bondverbindungen zu entwickeln, um zuverlässigere und langlebigere Leistungsmodule bauen zu können. Weltweit gibt es nur wenige Unternehmen, die diese Drähte herstellen. Vor diesem Hintergrund haben wir die Bimetall-Drähte eines Unternehmens getestet und festgestellt, dass sie sich für das Drahtbonden eignen.
Wegen der relativ dünnen Ummantelung aus Aluminium sind jedoch viele Halbleiterchips während des Bondvorgangs ausgefallen. Gemeinsam mit unseren Kolleg*innen am Forschungszentrum Strangpressen der TU Berlin wollen wir daher u.a. die Dicke dieser Aluminium-Ummantelung optimieren. Die Verbunddrähte werden hier im Institut getestet und systematisch analysiert. Wir hoffen, dass wir damit neue sehr zuverlässige Leistungsmodule bauen können.
Das Verfahren gibt es schon lange. Warum ist es noch relevant?
Die Drahtbondtechnik entstand Ende der 1950-er Jahre und wurde in den 1960er Jahren weiterentwickelt. Drahtbonden ist vielseitig einsetzbar. Vollautomatische Drahtbonder können so programmiert werden, dass nahezu jede geometrische Form auf der Oberfläche exakt hergestellt werden kann. Zum Vergleich: Bei der Embedding-Technologie kommt ein Laser zum Einsatz, um an die Kontaktpunkte zu gelangen. Das wird besonders schwierig, wenn auf großen Flächen (Panel) gearbeitet wird. Diese Schwierigkeit gibt es beim Drahtbonden nicht. Das macht diese Technologie so flexibel und so kosteneffizient. Nicht zu vergessen ist die Schnelligkeit – zwei oder drei Dickdrahtbonds pro Sekunde sind möglich.
Warum suchen Sie nach neuen Materialien für die Zukunft der Technologie?
Die Rückseiten von Leistungshalbleitern werden seit einiger Zeit nicht mehr gelötet, sondern mit hoch zuverlässigen Sinterverbindungen hergestellt. In der Vergangenheit war diese Chip-Rückseitenverbindung die Schwachstelle, da Lötstellen dazu neigen, eher zu versagen. Als mit dem Sintern begonnen wurde (was wir hier am IZM auch realisieren), wurden die Dickdrahtbondverbindungen auf der Chip-Oberseite zur Schwachstelle. Bei den üblichen 99,99 % hochreinen Aluminiumdrähten traten relativ schnell Ermüdungserscheinungen auf. Konkret entstehen diese Ermüdungsrisse, wenn thermomechanische Wechselbeanspruchungen auftreten. Letztendlich kommt es zum Abheben der Drähte und zum Ausfall des Moduls.
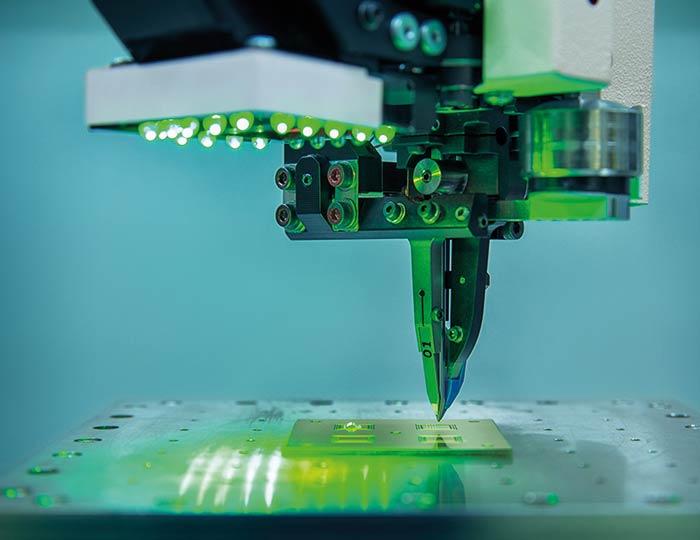
Bondkopf eines vollautomatischen Dickdrahtbonders beim Bonden auf einem Power-Modul-Substrat | © Fraunhofer IZM I Volker Mai
Was kann man tun, um das zu vermeiden?
Die Idee ist, mit neuen Aluminium-Kupfer-Drähten höhere Festigkeiten zu erreichen. Mit den bisherigen Alternativen aus Kupfer haben wir nur einen sehr geringen Yield (Ausbeute an funktionalen Chips) erzielt. Die auftretenden Kräfte waren zu groß. Viele Chips sind während des Bond-Prozesses gebrochen (Cratering). Deshalb wurden bisher keine zu Aluminium alternativen Materialien beim Bonden auf Chips in der industriellen Produktion eingesetzt.
In unserem Projekt wollen wir die Dicke des Aluminium-Mantels auf jenen Sweet-Spot einstellen, an dem die Chips nicht durch Cratering ausfallen und wir uns dem Best-Case-Szenario einer hundertprozentigen Ausbeute nähern. Andererseits soll der Kupferquerschnitt so groß wie möglich bleiben, weil Kupfer eine bessere elektrische und thermische Leitfähigkeit und eine höhere mechanische Festigkeit hat. Das Ziel des Projekts ist, die Materialzusammensetzung für den Einsatz für Leistungsmodule zu optimieren.
Man könnte also sagen, dass Kupfer die zentrale Rolle in diesem Materialmix spielt?
Kupfer ist wichtig, da es eine bessere elektrische und thermische Leitfähigkeit und eine höhere mechanische Festigkeit besitzt. Bei reinem Kupfer – wenn es ein Vollkupferdraht wäre – bestünde die Gefahr, dass die Halbleiter unter der sehr dünnen Aluminium-Metallisierung von drei bis fünf Mikrometern während des Bondprozesses beschädigt werden könnten (Cratering). Damit wären wir wieder bei Leistungsmodulen, die ausfallen.
Aluminium ist wichtig, weil es relativ weich ist und sehr gut bondbar ist. Genauer gesagt ist die Aluminiumschicht um den Cu-Draht auf die Aluminium-Metallisierung abgestimmt, die auf der Oberfläche fast aller Leistungshalbleiter zu finden ist. Zusammengefasst lässt sich sagen: Aluminium ist wichtig für den Drahtbondprozess. Kupfer ist wichtig aufgrund seiner elektrischen, thermischen und mechanischen Eigenschaften.
Gibt es noch alternative Materialien, beispielsweise Gold oder Silber?
Gold und Silber werden auch beim Drahtbonden verwendet, aber aus Kostengründen nicht für dicke Drähte. Die Unterscheidung zwischen Standard- und Dickdrähten ist sehr wichtig. Leistungshalbleiter werden wegen der hohen Ströme, die für diese Chips notwendig sind, ausschließlich mit Dickdrähten in der Wedge/Wedge-Technologie gebondet.
Der Durchmesser von Dickdraht liegt zwischen 100 und 500 Mikrometern. Standarddrähte sind in der Regel dünner als fünfzig Mikrometer. Sie werden meist mit dem Ball/Wedge-Bondverfahren verarbeitet. Die kleinsten Durchmesser liegen im Bereich von weniger als 15 Mikrometern. Vor zwanzig Jahren wurden sie fast ausschließlich aus Gold hergestellt. In den letzten zehn Jahren wurde aus Kostengründen bei vielen Anwendungen auf Kupfer und Silber umgestiegen.
Könnten Sie uns die Projektziele und die Aufteilung der Verantwortlichkeiten erläutern?
Am Forschungszentrum Strengpressen der TU Berlin werden die Verbunddrähte hergestellt. Sie werden stranggepresst, anschließend gezogen. Die Bonddrähte haben einen Durchmesser von zirka einem halben Millimeter. Sie bestehen aus einem Aluminiummantel um einen Kupferkern. Die Umformbedingungen werden durch numerische Prozesssimulation ermittelt. Die Ergebnisse validieren wir, indem wir sie mit Beobachtungen aus realen Umformversuchen vergleichen.
Am Fraunhofer IZM werden die mechanischen Eigenschaften der Bonddrähte durch Zugversuche und Härteprüfungen (Mikro-/Nanoindentation) bestimmt. Ferner ermitteln wir ihre Strombelastbarkeit und vergleichen sie mit anderen kommerziell erhältlichen Drähten. Zudem bestimmen wir die optimale Dicke des Aluminiummantels. Der Fokus liegt auf der Bondausbeute auf dem Halbleitermaterial (mit 100% Yield und ohne Cratering) und auf einer hohen Stromtragfähigkeit, die mit einem möglichst großen Kupferkern erreicht wird.
Mit einem Demonstrator-Setup für industrielle Drahtbondanlagen führen wir gemeinsam mit unseren Industriepartnern Hesse GmbH und Vitesco Technologies GmbH Bondtests durch und passen die Anlagen und Tool-Geometrien entsprechend an. Schließlich führen wir Temperaturwechsel- und mechanische Belastungstests als Teil unserer Zuverlässigkeits- und Lebensdauer-Untersuchungen durch.
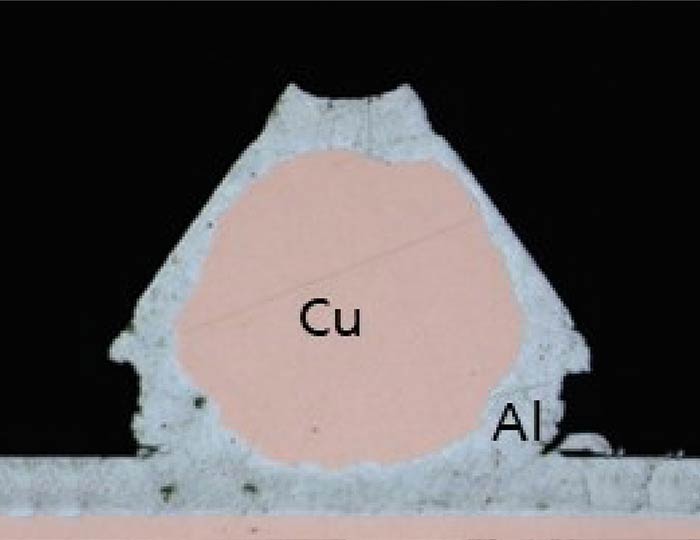
Schwerer Draht Al-Cu-Bi-Metall Bondkeil | © Fraunhofer IZM
Welche Erkenntnisse soll das Projekt liefern?
Aus wissenschaftlicher Sicht könnten die Analysen der Prozesskette Strangpressen und Drahtziehen eine weiterführende Prozesskette anstoßen, um dadurch die Materialeigenschaften zu verbessern. Mit unseren mechanischen und thermomechanischen Untersuchungen zeigen wir neue Bimetall-Kombinationen für Bonddrähte auf. Diese könnten den Anforderungen der Leistungsmodule der Zukunft gerecht werden, indem sie beispielsweise höheren Temperaturen standhalten. Die aus diesem Projekt gewonnenen Erkenntnisse werden eine wichtige Grundlage für die Herstellung und die Verarbeitung von Aluminium-Kupfer-Bonddrähten sein.
Wie sieht es aus kommerzieller Sicht aus?
Die Aluminium-Kupfer-Bonddrähte, an denen wir arbeiten, sind für den Einsatz in Leistungselektronikmodulen gedacht. Leistungselektronik wird beispielsweise in Wandlern eingesetzt, die den aus Wind- oder Solarenergie erzeugten Gleichstrom in Wechselstrom umwandeln, der in unser Stromnetz eingespeist werden kann. Leistungselektronikmodule können einen wichtigen Beitrag zu unseren Bemühungen leisten, unseren CO2-Fußabdruck zu reduzieren, da die verlustfreie Umwandlung einen geringeren Energieverbrauch verspricht. Das gilt auch für Wandler im Bereich der Elektromobilität. Damit die heutigen und zukünftigen Elektroautos alle Funktionen bieten, die wir erwarten, wie autonomes Fahren, müssen wir Gewicht einsparen, die Leistung steigern und/oder ihre Komponenten verkleinern.
Wie sieht die Zukunft des Drahtbondens aus? Wird diese Technologie auch in fünfzehn Jahren noch relevant sein?
Ich kann Ihnen eine Anekdote dazu erzählen: Als ich vor 22 Jahren hier am Fraunhofer IZM begann, sagte der damalige Leiter und Gründer des Instituts, Professor Reichl, zu Professor Lang, seinem späteren Nachfolger und damals Leiter der Drahtbond-Gruppe, dass er anfangen sollte, nach einem neuen Forschungsthema zu suchen, weil Drahtbonden bald tot sei. Dennoch sind heute nach grober Schätzung über 75 Prozent der mikroelektronischen Produkte drahtgebondet, eben weil diese Technologie so flexibel und kostengünstig ist.
Ich gehe davon aus, dass diese Technologie auch zukünftig relevant bleiben wird. Das Drahtbonden wird signifikante Fortschritte mit dünneren Standarddrähten machen, unterstützt durch eine größere Auswahl an verschiedenen und hochpräzisen Maschinen. Innovationen geschehen bereits, insbesondere in den Bereichen der Flip-Chip-, Chiplet- oder Embedding-Technologien. Aber all das wird Zeit brauchen.
Add comment