In factories, cars, agriculture, medicine – microsystems are used everywhere. Julia Günther-Sorge, a researcher on microperipheric technologies at the Technical University of Berlin and member of the Sensor Nodes & Embedded Microsystems group working in cooperation with Fraunhofer IZM, has met with us to explain how these microsystems work and which potential they can have for certain applications.
RealIZM: Can you start by giving our readers a sense for where the research at Fraunhofer IZM is heading in terms of smart microsystems?
Julia Günther-Sorge: In our department, RF & Smart Sensor Systems, we are designing smart sensor systems and RF components for integration – as subsystems, as part of something bigger, let it be a car, a production facility, or even a human being. This means that everything revolves around sensor systems and radio transmissions. In terms of progress with interconnect technologies and our interdisciplinary cooperation here at the Institute, we are able to optimize these systems from many very different points of view, e.g. reliability or miniaturization.
The expectations get tougher when it comes to firmware/software implementation and the functional design. With every added feature, the system gets more and more complex, and its specifications have to be weighted differently for an optimum trade-off. Mostly, the trade-off is between energy, size or space, and data volume in a desired range. Trends like IoT, Industry 4.0, or 5G bring about many new solutions, all of which depend on the right infrastructure. The more intelligent the sensor systems are, the more autonomously and independently systems can operate.
RealIZM: You offer a complete one-stop solution from the design to the first prototype, plus software? This sounds to us like genuinely custom-made solutions.
Julia Günther-Sorge: Exactly! Our customers’ requests are often very specific, compared to the subjects that I work with in funded projects, and our research covers a quite broad field. Our customers often wish to know which systems are available, which fit best, and which can simply be purchased right away. However, most of the actual effort happens when we implement smart sensor systems into their target environment. It is about making them fit with the interfaces in terms of both hardware and software.
At the same time, development cycles have become shorter and shorter in recent years. In order to accelerate the work of our group, we have started to use modular systems. Some types of sensors (such as acceleration or temperature sensors) are needed very often, so we already have the right hardware and software interfaces ready for these components. As many systems are supposed to be particularly small, or special sensors are required, we can quickly move on with adapting the modules. What matters next is the requirements for the microcontroller and the data processing happening in the system.
At this point, important decisions have to be made to make the overall design of the smart sensor system successful – whether the system provides the computing power itself or not. If this is the case, data gets processed directly, which means that you need less energy to transmit great volumes of data. But the data could also be sent to and processed by another system. This can lead to problems with energy management, as it costs a lot of energy. This is an interesting scientific question: to make an objective decision about which method is the better choice.
Which priorities have to be considered? Which components are critical? How to configure the connection of the sensors to the physical environment?
The firmware’s design has an impact on energy management, as well. And it must be taken into account that there are different radio standards that can be used for smart sensor systems. Some industrial projects partners use LoRaWAN, others WLAN, Bluetooth, or GSM. This means different frequencies, different antennae, and different advantages or disadvantages. For these radio standards, you usually have set communication protocols, but part of our group also works on optimizing proprietary protocols in order to make systems more power-efficient for the application in question.
We tend to work on more specialized applications that require specific solutions, which is why most project teams are interdisciplinary and deal with different topics. We rarely have an issue that we would only pursue in a single direction.
RealIZM: What is your part of the research work?
Julia Günther-Sorge: My research work relates to smart sensor systems for higher operating temperatures, in ranges up to 250°C, focussing on the PCB design and layout parameters and the overall functionality. It’s not always possible to use important system components like batteries, energy management systems, microprocessors for data processing, RF front ends, or MEMS sensors. That makes it crucial that potential is gained from the application environment and the interfaces available for the system.
Sometimes, the system has to be particularly cost-effective or needs to use special technologies that are particularly robust. One example from our projects in agriculture was about optimizing the silage process by developing wireless sensor nodes for capturing data within silage. One difficulty was that the housing had to be specially designed to withstand wheel loaders driving on top of it. In addition, there were special environmental conditions for the radio link, as the data had to be transmitted through silage. We also developed a measurement technique that uses two radio transceivers to measure the density of the silage. The project was funded by the Federal Ministry of Food and Agriculture (BMEL) and the FNR, as the central coordinating agency for renewable resources in Germany.
RealIZM: What sizes are we talking about?
Julia Günther-Sorge: The smallest system using conventional technology is not even one centimetre on each side. But there are also systems with a length of several decimetres, which depends on the application, such as high-voltage line monitoring or condition monitoring in general. Provided that components are available as bare dies, and thanks to the cooperation between Fraunhofer IZM and the TU Berlin’s research group Microperipheral Technologies, we are able to design parts of the system at various technology levels, such as system-in-packages or multi-chip modules, to miniaturize and integrate sensor systems.
RealIZM: What advantages do these microsystems offer?
Julia Günther-Sorge: The sensor systems can be integrated to provide add-on functionality to machine parts in production or to industrial goods. These systems are mainly there for data acquisition. They can do so in harsh environments, even though that means that the measuring systems themselves have to withstand high temperatures or heavy mechanical loads, for example. Standard printed circuit board technologies are often not tough enough for this. A combination with high-performance materials, e.g. for high-frequency transmission for on-board antennas, is a great benefit for system performance. Each layout can be optimized specifically for the target system it is meant for. Sometimes, special extras are also required, such as GPS, fingerprint capturing, or RFID features.
RealIZM: What are the main developments that you can see coming for microsystems?
Julia Günther-Sorge: I see an important trend in that more data is being shared with lower energy consumption. The keywords here are 5G and the Internet of Things, IoT, as mentioned before. More and more wireless sensor systems are being integrated into systems for better performance, and more features, making e.g. autonomous driving possible. In the future, artificial intelligence will be part of smart systems. The compression and processing of the vast amount data required for this is another field that needs to be addressed. The systems have to be able to analyse the raw data and extract the relevant information.
RealIZM: What is the potential of microsystems?
Julia Günther-Sorge: Think about industry: There is great potential in terms of avoiding incorrect operating or process states, which can help reduce the maintenance costs for machines or other facilities. I see great benefit, generally spoken, in measuring process parameters, like vital data acquisition, whether from machines, agricultural processes, or even athletes, just for process optimization. By monitoring various factors, processes can be optimized, leading to better efficiency. In the end, this helps us use our resources more efficiently.
Better data can help us assess a machine’s or a person’s health, e.g. to recognise potential hazards for people in physically dangerous work, like firefighters. Another important field is data security and plagiarism. We need to take care and ensure that no security risk arises from sensor systems sharing data wirelessly.
RealIZM: How can people get in touch and start working with you?
Julia Günther-Sorge: My group is always searching for collaboration projects and partners in different areas of application. In particular, we’re interested in condition monitoring or ideas that can bring environmental benefits by reducing the consumption of resources, but also in health or safety issues.
IT CAN BE ALSO INTERESTING FOR YOU:
- Modular Electronics – A Sustainable Solution For The Smartphone Era?
- Smart Farming: Facilitating Change For Pharmacy, Medicine, And Nature
- How Waterproof Flexible LED Systems Became a Reality
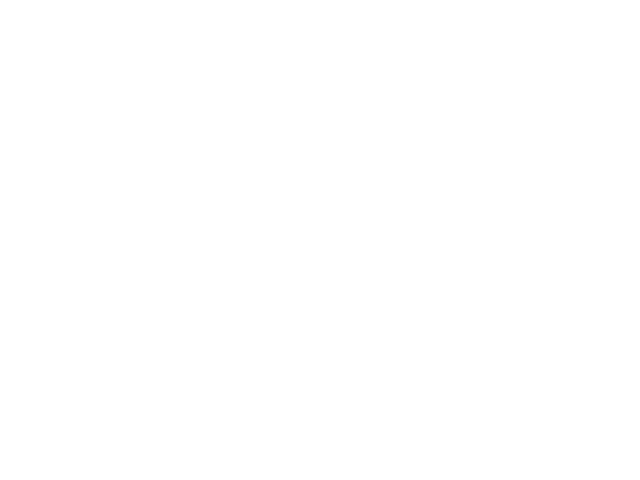
ปั้มไลค์ says:
Like!! Great article post.Really thank you! Really Cool.