Metallic interconnections can be hard, not only in the literal sense, but also figuratively speaking. This is why a whole research group at the Fraunhofer IZM is dedicated to understanding how to solder and sinter properly. Power electronics have upped the stakes when it comes to operating temperatures, thermal conductivity, or the durability of electrical components and systems. We seized the opportunity to sit down with one of our scientists, Olaf Rämer, to talk about the technologies behind metallic interconnections.
RealIZM: Olaf, tell us a bit about yourself.
Olaf Rämer: I’m working in the Metallic Interconnection Technologies (MIT) group at the System Integration & Interconnection Technologies (SIIT) department of Fraunhofer IZM. The question that keeps us busy is: How we can master the demanding requirements in assembly? Our goal is to understand and research deep into the effects at the interconnection layers. The main technologies at MIT are soldering, sintering, and wire bonding processes. Since I have my degree in materials sciences, I find the large number of different materials and the variable parameters in these processes very interesting. It’s like a huge landscape with a lot to discover, and you can always go looking for the best path to maximum performance. What I enjoy most at Fraunhofer IZM is the large spectrum of different projects and challenges, on the one hand, and, on the other hand, the easy and direct line of communication with experts from many different fields.
RealIZM: Can you explain to us why specifically we need these processes and which materials are used?
Olaf Rämer: Basically, metallic interconnections are chosen for their high thermal conductivity, heat resistance, and reliability. Together with their electrical conductivity and strength, they are the optimal choice for many applications. When it comes to the soldering process, many people remember lead-based solder. However, lead use has decreased massively since the European RoHS directive banned it. Tin-based solders are used primarily today, such as tin-silver or tin-silver-copper solders. All alloys are characterized by their unique melting points, which also means different operating temperatures and other characteristic properties.
Gold-tin solder with 80 % gold content is an important material for special applications, in particular for higher thermal loads, where lifetime concerns and high geometric precision come into the picture. For example, it is used in laser diodes for signal amplification in submarine cables. Because maintaining such a cable is very expensive or sometimes even impossible, the components have to work for as long as possible.
These tin-based and gold-based solder joints have very different properties, since the former is ductile, but the latter, the gold-based joint is very hard. Its hardness means that you have to consider measures to prevent cracking, but you can get really high reliability if it’s done correctly. Tin-based solders are more commonly used in mass applications that are not exposed to high temperatures.
One of the most promising technologies today is silver sintering, which finally found its way into the industry several years ago. Silver-sintered interconnections will melt at over 900 °C, which is quite a bit hotter than any semiconductor structure could handle. However, the process is more difficult to control compared to soldering, especially with larger areas where you have to pay attention to more parameters to get an optimal interconnection.
RealIZM: What are the main challenges and goals in your work?
Olaf Rämer: It is challenging to find the optimal process and the optimal combination of materials to match your product’s requirements. Furthermore, an important part of our job is to find the root cause in case of a failure. The main goal of our work is to improve on the good properties, most importantly, to allow higher application temperatures. Additionally, in the field of optoelectronics, the goal is to increase service life and precision, which is particularly important in optical applications like the submarine cables I mentioned. In general, the usability and reliability of processes also matters, e.g. interconnecting larger areas while minimizing the defects.
RealIZM: What are typical tasks that you have to deal with in your day-to-day work?
Olaf Rämer: One obvious thing that comes up frequently is failure analysis, whether it is because a client asks us to do so or because we want to inspect our own samples.
Far more complex tasks include creating and testing concepts for assembling structures that you cannot do with off-the-shelf processes, even if they look good in a draft. Then your job is to identify all the potential pitfalls and to create tweaks and workarounds to handle the problems. A mismatch of your components’ thermal expansion coefficients would be one typical issue, where I’d need to adjust the designs and processes in order to keep resulting stresses at bay.
In hands-on terms, this means I use our full analysis and assembly toolbox, including cross-sectioning and microscopy, SEM, X-rays, C-SAM, XPS, thermal cycling, using die bond machines, solder ovens, sintering presses, and so on.
RealIZM: Can you tell us more about some of your research?
Olaf Rämer: For example, we did a study on the life expectancy of transient liquid phase bonding (TLPB) compared to other interconnection techniques. We built die attaches using a range of materials and then subjected them to thermal cycling, which induces mechanical stress and leads to failure after a number of cycles. This simulates the stress these structures would have to endure over their lifetime. What we found was that the common tin-silver solder has the shortest lifespan. Silver sintering with added pressure already shows a much longer life, with higher pressures resulting in increased lifespans. You get the longest life with the copper-tin system in TLPB. It endured for more than eight times as many cycles as the regular tin-silver solder did. So the production process and the proper selection of materials have a huge impact on the reliability of a product.
RealIZM: You spoke about pressure being applied during sintering. How does that work with electronics?
Olaf Rämer: That is one of the issues with this particular method. Generally speaking, the more pressure you apply, the better your two surfaces are connected, i.e. porosity is lower in the interconnection area. But as you said, you are rather limited in that regard when you work with delicate electronics. It is hard to give a general answer for that, but what you try to do is to apply as much pressure as you can without damaging anything. The specifics vary greatly based on the structures that you are using, so a lot of work goes into adjusting our methods to the specifics of each given project.
RealIZM: Going from the process to the product: Which sectors are mainly using the products you are working on?
Olaf Rämer: The two most important areas of application are power electronics and optoelectronics. E-mobility is a very prominent area of application, but they are also used particularly for renewable energies, where they convert the electricity so that it can be fed into the grid. In the field of optoelectronics, it’s mainly attaching laser diodes where you need high quality interconnection technologies, for example in laser cutting machines in mechanical engineering.
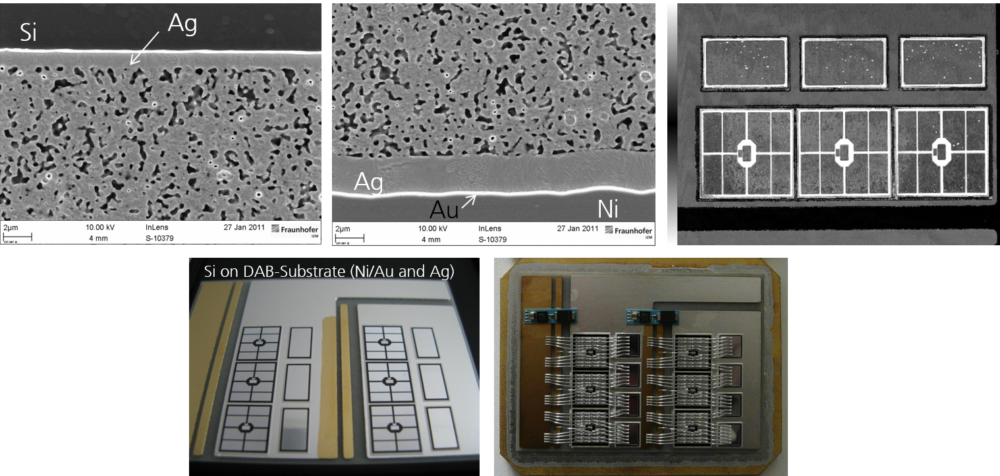
RealIZM: Can you tell us about one of the projects you were working on?
Olaf Rämer: One very interesting project was a BMBF-project called KorSikA. Basically, it was about silver-sintered interconnections in the power electronics for wind power plants. The goal was to answer the question whether salty air in maritime environments damages the silver-sintered compound. More specifically, we examined various silver-sintered compounds for their corrosion properties. Another, smaller project was about developing a soldering technology for a small cap that shielded a very delicate sensor in a protective atmosphere.
RealIZM: Would you say that there is something unique about your group or about Fraunhofer IZM in general?
Olaf Rämer: There is. One special competence of our group is gold-tin soldering. But more generally, what is special here at Fraunhofer IZM is that packaging is not just a secondary issue, as it often is in industry, but the main focus. That leads to a high concentration of expertise and creates a great environment for innovations. If, for example, different interconnection technologies have to be combined in a complex structure, e.g. not only metallic interconnections, but also bonding, or if there are unusual mechanical or thermal loads, then you can simply go to other experts in the office next door and discuss your ideas. We have groups that are specialized in the design of power electronics, another in simulations, and so on. In addition, there is an abundance of test opportunities right here at the Institute and the means to construct and build complete demonstrators.
RealIZM: Can you give us an outlook into the future? What new technologies are on the rise?
Olaf Rämer: I would see power electronics in e-mobility as a large field of application for our future research. In general, the power electronics market is growing, and there are still many opportunities to save a lot of energy through improvements and innovations. Silver sintering is currently the best technology for attaching power semiconductors. It is used in industry and is characterized by a long service life, high current carrying capacities, and great thermal conductivity – on top of the very high operating temperature limit. However, silver is not a particularly cheap resource, which is problematic for mass production. Therefore looking for alternatives will become increasingly important. Recently, copper sintering has come into the focus of research, because it has comparatively good electrical and thermal properties and is much cheaper than silver. However, copper oxidizes relatively quickly, which creates considerable challenges for the sintering process. There are plenty of ways to cope with the properties of copper: with chemical additives, sintering with adjusted parameters, or other approaches like modifying the copper particles. Finding the best solutions and understanding the specific interactions of factors will be part of our future work.
Generally, I am optimistic about developments in our field of research. In terms of electrical and thermal properties, metallic interconnections are virtually impossible to substitute, and with the continued spread of electronic devices in our lives, they will become even more important.
IT CAN BE ALSO INTERESTING FOR YOU:
- Modular Electronics – A Sustainable Solution For The Smartphone Era?
- Pixel Detectors – The Smallest Pieces In The World’s Largest Particle Collider
- Smart Farming: Facilitating Change For Pharmacy, Medicine, And Nature
- How Waterproof Flexible LED Systems Became a Reality