To improve and enhance the performance of high-performance sails, it is important to know and optimize their fluid mechanical and structural properties. For ultralight textile structures – be it sails for ships or even paragliders and parachutes – it has been almost impossible to verify simulation results directly or meaningfully. There has been a lack of measurement systems suitable for the nature of these systems. These textiles are extremely light, supple, and flexible. Measurement technology, on the other hand, tends to be heavy, rigid, and firmly mounted.
Lars Stagun from the Technical University of Berlin tells us about the art of making the impossible possible. As head of the SenSail research project, he was responsible for integrating an ultralight sensor system into the surface of a high-performance sail in order to record fluid mechanical measurement data on the spot.
RealIZM: One focus of research at TU Berlin and at Fraunhofer IZM is to integrate electronic functions into textile surfaces. What distinguishes the SenSail project from previous research work, and how did this project idea come about?
Lars Stagun: A former colleague of mine at the Technical University of Berlin is a passionate yachtsman and came up with the idea for the project in cooperation with ISTEC AG, a leading manufacturer of downwind sails. I joined later as project manager. Before then, sailing boats were terra incognita for me. That made it an unforgettable experience for me to take part in the final test on an actual sailboat. The test took place on Lake Brombach near Nuremberg in Germany. Our project partner keeps a vessel on the lake.
I was not the only one who broke new ground in the project. It was also a first for our research team: the downwind sail is the largest textile we have worked with so far. Normally, we work on smaller textiles, the size of clothes you can wear. For SenSail, we had to equip an approximately 80-square-meter textile surface with ultralight measurement systems and develop a suitable textile bus structure for it.
The project ran for a period of three years from 2018 to 2021, as part of the Central Innovation Program for SMEs (ZIM).
RealIZM: Is the effort worthwhile, installing actual microsensors in large-scale textiles when simulations and modeling are available?
Lars Stagun: It is true that the simulation of fluid mechanical processes is now a standard procedure in the development of new systems. However, in order to evaluate the quality and reliability of such predictions, it is very important to be able to compare simulations with real measured data.
It is an enormous competitive advantage if unnecessary iterations in product development can be avoided. With our textile measurement system, we are making an important contribution to checking and ultimately improving the validity of simulations for ultralight textile structures.
RealIZM: Is your research project limited to sailing or are other application scenarios also conceivable?
Lars Stagun: Our findings form an important basis for the application of almost all lightweight and ultralight textile structures that could not previously be evaluated in terms of fluid mechanics.
With the help of our ultralight measurement system for fluid mechanical data acquisition, the simulations carried out in advance for the high-performance sail could be checked for the first time and their quality and significance analyzed. Our project partner is now able to make well-founded decisions based on actual measurements when improving existing products. With the acquisition and analysis of fluid mechanical measurement data directly on the sail’s surface, ISTEC is taking on a pioneering role. In the long term, this could be used to get an edge in the market and maybe explore new product fields. The expansion of the product portfolio to new classes and categories of sails or even parachutes would be a conceivable option.
There are also numerous possible applications outside the field of nautical engineering. Architectural membrane materials and adaptive textiles are already being used as temporary or even permanent installations in soccer stadiums, stations, and airports as coatings, claddings, or canopies. Collecting measurement data for such large and complex textile structures has so far been very complex. There are hardly any integrated sensors available, if at all. In addition, modeling and simulations involve enormous engineering and computing effort.
Manufacturers of ultralight sail systems in the architectural field could use fluid mechanical data to significantly shorten their development cycles, save costs, and realize innovative systems that would previously have been considered unmanageable. The new measuring system could also be used with decorative or functional lighting systems, heating elements for de-icing, for example, or even interactive textile-bracing systems for or on textile facades.
RealIZM: In essence, only people who measure data can make good predictions. The same is true in meteorology. Which measurement data are relevant for comparing the simulations on sails?
Lars Stagun: Our task was to measure the temperature effects, air flow, and air pressure at the different heights of the sail. In addition, the force influences were to be recorded at the three anchor points – sail head and the two clew horns – of the 20-meter sail.
The headsail is a complex system in how it interacts with the ship, the dynamics of the weather, and the sea. We therefore had to ensure that we also recorded the movements of the headsail and the orientation or stance of the Parasailor. That is why we also used inertial sensors. For individual points on the sail, this let us determine the orientation and acceleration with the nine classic degrees of freedom the sensors deliver.
RealIZM: What challenges did you have to consider for the sensor technology?
Lars Stagun: When selecting the measurement technology and the method of attachment, we had to remember to not damage the sail and to influence its properties as little as possible. As experts in microelectronics, selecting and producing ultra-light sensor modules was no problem for us. For airflow sensing, we selected miniature flow meters with a size of 15 mm x 5 mm x 5 mm and a weight of < 5 mg. The force sensors we used each had a weight of under 40 g.
The challenges were of a different nature. Our project partner made a special sailcloth according to our requirements. We were then responsible for integrating the sensor technology into that textile. The question of how to attach the sensor technology to the textile in a functional way was particularly exciting. To do this, we had to lay a 50-meter textile-based conductor route via channels on the sail. These channels were made of the same material as the sail and were splash-proof. Building such a long bus structure and developing a suitable robust bus protocol was a first for our team.
This also needed physical effort. The main module had to be soldered directly to the conductor laid within the sail channels. To do this, I laid down directly on the sail prepared in our hall, with soldering iron in hand: A work situation you don’t find yourself in that often.
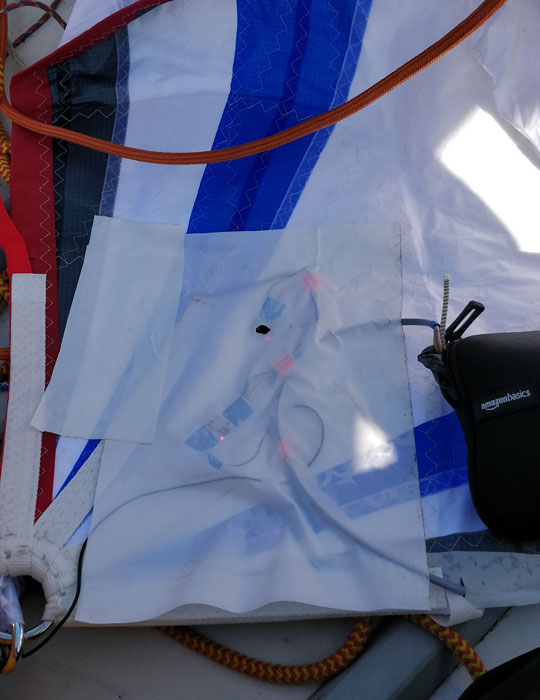
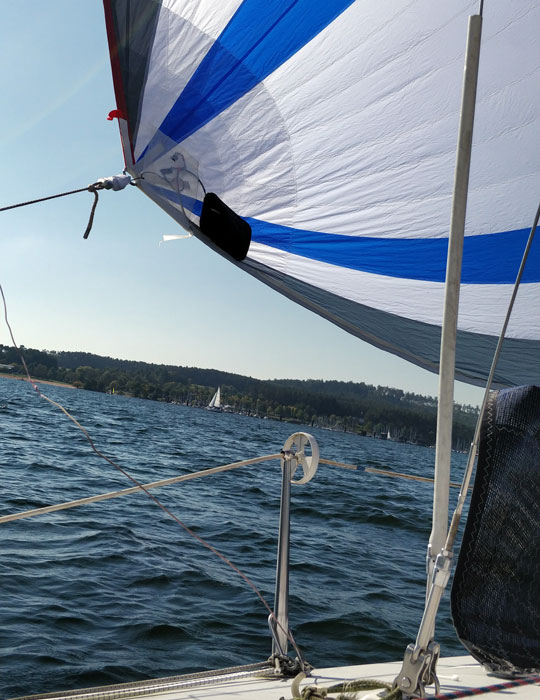
RealIZM: How was the bus system set up to ensure the acquisition and evaluation of the measurement data?
Lars Stagun: Ensuring the communication of over 19 sensor nodes via channels over 50 meters, controlling them, and collecting sufficient measurement data was challenging. We had a specific topology to help us lay a flexible and highly conductive textile tape over channels across the entire sail.
In addition, we had to have a reliable connection from the individual sensors via the channels. We did this by equipping the electronic modules with our own textile bonding technology. There was one board each for force measurement, the 3D inertial sensors with temperature and air pressure, and the flow sensors.
The evaluation of all analog signals was done directly on the modules. All data was collected in a main module and forwarded wirelessly to a central evaluation unit.
RealIZM: Was the central evaluation unit located in the hull of the ship or also on the sail?
Lars Stagun: The main unit collecting all data and the sensor bus system had to be self-sufficient with portable power supply and was sewn into a small pocket at the anchor points of the sail. It transmitted all measurement data collected on the sail surface via WLAN to a central evaluation unit. This was located in a robust and portable hard case and consisted of a screen, keyboard, and mouse. It was important to install the technology in such a way that it was splash-proof when the case was open. We also had to make provisions for the unlikely event that the case goes overboard. We prepared the case to be watertight when shut.
RealIZM: How did you ensure wireless communication, and how long was the measurement system operational?
Lars Stagun: The system was both self-sufficient and energy-efficient in operation for a period of up to eight hours. We were able to track, live and at any time, with a screen and keyboard how the individual sensors were working and what readings they were taking. Furthermore, we were able to store the values together with a time stamp for later evaluation when back on land.
We put in wireless communication to a Raspberry Pi. Its power consumption was relatively low and, at the same time, offered sufficient performance. In addition, a power bank and an extremely energy-saving screen were used.
RealIZM: The SenSail project was completed successfully. What’s the next step for you and your team?
Lars Stagun: My team and I are very proud that everything from the textile integration to the wireless transmission and evaluation of the measured data worked smoothly at SenSail. On a positive note, we were able to generate added value across projects.
First, we now have the practical knowhow to integrate ultralight sensor technology reliably and splash-proof in large-area textiles. Second, we were able to gain initial practical experience about how long communication distances can be realized in fabric. It is also important that we can now successfully transmit measurement data wirelessly, visualize it, store it for several hours, and then evaluate it.
A wide range of applications are certainly conceivable in the field of wireless data transmission. It would be great if VR glasses could transmit all high-resolution data wirelessly in the future. Who wants to have cables everywhere? Cable clutter and limited freedom of movement are annoying.
I’m currently partially involved in a project in the medical field. This involves special rehabilitation suits equipped with electronics for helping hemiparesis patients. Wireless freedom would be a great advantage for their possible applications, not least from the user’s point of view.
RealIZM: … are you now also an enthusiastic sailor?
Lars Stagun: I don’t have a sailing license yet, but I do have a motorboat license.
This interview was conducted by Jacqueline Kamp and edited by Katja Arnhold.
Pictures and Video: Lars Stagun, TU Berlin
This could be also interesting for you:
- Helping Self-Driving Cars Recognize Objects With Cameras and Radars Combined
- Turbotesting with Lab-on-a-Chip for Point-of-Care Diagnostics
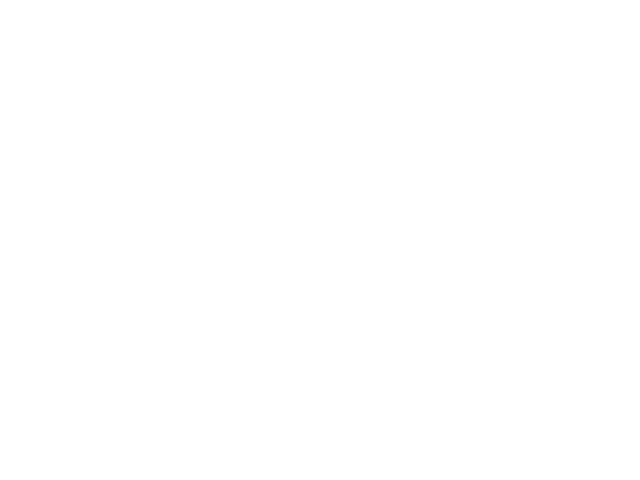